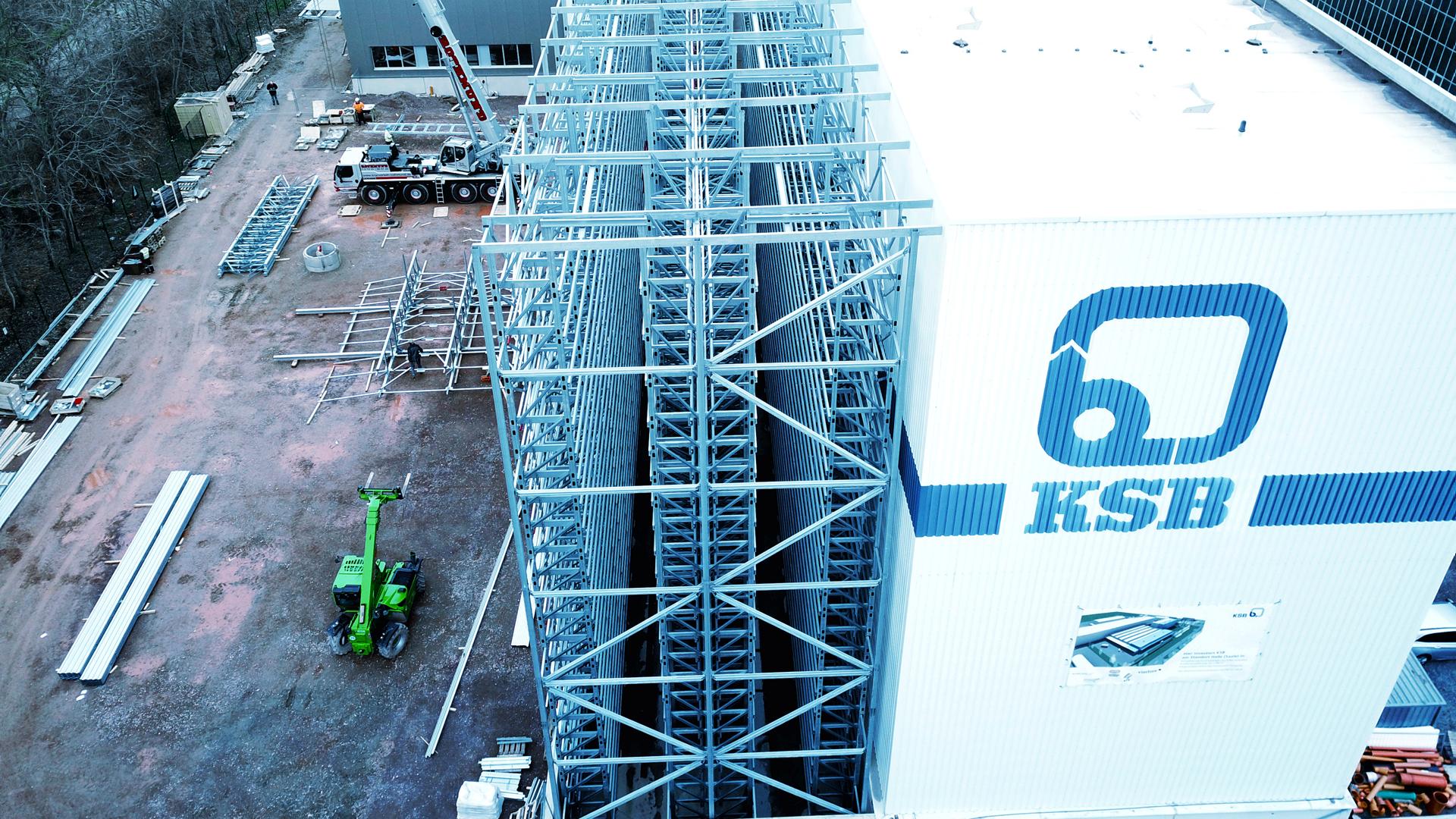
In großen Schritten zu 25 Prozent mehr Leistung
Ein Füllgrad von über 97 Prozent, wenig Raum für Material-Puffer in der Produktion, hohe Erwartungen der Kunden – das im Jahr 1995 in Betrieb genommene Produktionslager von KSB am Standort Halle (Saale) war an seine Grenzen gekommen. „Der Standort Halle ist das Kompetenzzentrum von KSB für Pumpen und Tauchmotoren für unseren Bereich Wasser- und Abwassertechnik“, erklärt Werksleiter Frank Aschenbach. Angetrieben von der wachsenden Weltbevölkerung, der Urbanisierung und dem zunehmenden Umweltbewusstsein ist das ein echter Wachstumsmarkt. „Wir produzieren jährlich rund 12.000 Pumpen und 16.000 Tauchmotoren – mit hoher Fertigungstiefe und extrem großer Variantenvielfalt. Mit dieser Stückzahl stoßen wir allerdings an die Kapazitätsgrenzen.“ Deshalb investiert KSB in Halle bis 2022 rund zehn Millionen Euro in die Lagerlogistik und in die mechanische Fertigung.
„Um dem Wachstum und den steigenden Anforderungen unserer Kunden nach kurzen Lieferzeiten gerecht zu werden, entwickelten wir uns am Standort strukturell weiter“, ergänzt Marcel Schwarze, KSB-Projektleiter für die „Halle 2020“ genannte Werkserweiterung. Hierfür wurde neben dem Ausbau der 24.000 Quadratmeter umfassenden Produktionsfläche, der Beschaffung größerer Fertigungsmaschinen und der Optimierung der Arbeitsabläufe auch die Modernisierung und Erweiterung des Hochregallagers geplant. Dieses ist das Herz der Produktion und versorgt die Maschinen und Fertigungslinien mit Rohware und Halbfertigteilen.
Wachstum führte Logistik an ihre Grenzen
Deshalb sind reibungslos funktionierende und leistungsfähige Lager- und Materialfluss-Prozesse für das Unternehmen unabdingbar. Denn kaum eine der gefertigten Pumpen gleicht der anderen – daher produziert KSB sie nicht etwa auf Vorrat, sondern auftragsbezogen und versendet sie dann direkt. Gelagert werden die Roh- und Halbfertigwaren in Palettenboxen. „Von den mehr als 5.900 Palettenstellplätzen waren zu Spitzenzeiten nur noch wenige frei“, schildert Oliver Fuchs, Lagerleiter am Standort Halle, die Situation im Hochregallager. „Um Platz zu schaffen, mussten wir regelmäßig umpacken und verdichten. Das ging sogar so weit, dass in der Spätschicht zwei Mitarbeiter mehrere Stunden mit dem Verdichten beschäftigt waren, damit am nächsten Morgen wieder etwas Platz war.“ Und das, obwohl das Unternehmen bereits externe Lagerkapazitäten in der Nachbarschaft angemietet hatte.
Hinzu kam die Verschlankung der Produktion, wie Fuchs erklärt: „Früher haben wir an den Pufferplätzen in der Produktion Material für zwei Tage zwischengelagert.“ Doch mit der Zunahme der Aufträge wurde dieser Platz für die Fertigung gebraucht. Heute muss das Team von Oliver Fuchs das Material innerhalb von vier Stunden oder kürzer in der Produktion bereitstellen. „Durch die massive Auslastung des Lagers hatten wir einen logistischen Mehraufwand von 30 bis 40 Prozent“, überschlägt Norbert Fisch, der als Prozessoptimierer von KSB die pünktliche Lieferung am Standort Halle sicherstellt. „Wir wollen und müssen auch in Zukunft weiter wachsen“, schildert Fisch. „Daher war die Frage, wie wir uns schnellstmöglich besser aufstellen können.“
Die Entscheidung fiel auf eine Erweiterung und Modernisierung
Die erste Idee war das Upgrade des Lagerverwaltungssystems. Bis dato hat das mehr als 20 Jahre alten Warehouse Management System (WMS) viadat 5.4 das Lager und den Materialfluss gemanagt – die Software des Stuttgarter Intralogistik-Experten viastore, der auch das Hochregallager gebaut hatte. Dieses WMS beinhaltet viele Funktionen noch nicht, die in der aktuellen Generation 9.1 selbstverständlich sind. „Mit dem Upgrade hätten wir die vorhandenen Plätze besser ausnutzen können“, erläutert Fisch. Doch schon bald zeigte sich, dass ein neues WMS allein nicht ausreichen würde. Denn auch die Prozesse in der Fördertechnik, die das Material vom Hochregallager zu den Kommissionierplätzen transportiert, erwiesen sich bei der gewachsenen Auftragslage als Nadelöhr.
Daher entschloss sich KSB dazu, im Rahmen einer Werks-Restrukturierung das dreigassige Hochregallager um zwei zusätzliche Gassen mit insgesamt 4.600 Stellplätzen zu erweitern, die Fördertechnik zu optimieren, die Steuerungen zu erneuern sowie auf Profinet als Bussystem umzustellen. „Dabei war es uns wichtig, den gesamten Umbau ohne Beeinträchtigung der Produktion zu realisieren“, betont Fisch. Den Auftrag dazu erhielt viastore – nicht nur, weil das Unternehmen bereits die ursprüngliche Anlage gebaut und diese regelmäßig modernisiert hatte, wie Norbert Fisch ausführt: „Wir haben uns für viastore entschieden, weil das Unternehmen neben der System-Kompetenz auch die Steuerung und die modernste Software für Lager und Materialfluss mitbringt. Zudem hat viastore uns von der Planung über Simulation und Prozess-Optimierung bis zur Durchführung begleitet und uns einen erfahrenen Projektleiter zur Seite gestellt, der uns jederzeit Sicherheit gab. Damit konnten wir uns auf unsere Kernaufgaben konzentrieren.“
Das Ziel: 25 Prozent Leistungsplus
Als Ziel der Erweiterung und Modernisierung definierte KSB eine Leistungssteigerung von 25 Prozent. In Zusammenarbeit mit dem KSB-Team entwickelte viastore verschiedene Szenarien und überprüfte diese mithilfe umfangreicher Simulationen auf ihre Praxistauglichkeit und Rentabilität. „Schließlich entschieden wir uns für das Konzept mit den besten Ergebnissen“, schildert Norbert Fisch.
Daraufhin machte sich Martin Ziemann, Projektleiter bei viastore SYSTEMS, an die Feinplanung – immer unter der Vorgabe, die laufende Produktion nicht zu unterbrechen. „Als erstes erstellte er einen detaillierten Zeitplan mit allen erforderlichen Arbeitsschritten. Alle Gewerke bis hin zum Brandschutz und dem Fassadenbau waren zum Teil minutengenau durchterminiert“, erinnert sich Norbert Fisch – und staunt noch immer: „Dieser Zeitplan mit insgesamt 189 Prozessschritten musste im Laufe des Projekts nur einmal angepasst werden – und das auch nur wegen Probleme beim Baugrund.“ Marcel Schwarze ergänzt: „Jeder einzelne Umbauschritt war damit im Vorhinein festgelegt, und jeder Beteiligte wusste genau, welcher Schritt wann umzusetzen ist.“
Stufenweise zum Retrofit
„Nur mit einer solchen Vorgehensweise können wir Ausfälle in der Produktion vermeiden“, verdeutlicht Swen Mantel, der bei viastore für das Retrofit-Geschäft verantwortlich ist. „Bei derartigen Maßnahmen muss man stufenweise planen – insbesondere um das Risiko für Unterbrechungen des laufenden Betriebs zu minimieren.“ Um alle Prozesse aufrechtzuerhalten, realisierte viastore immer wieder temporäre Zwischenlösungen. „Die drei Kommissionierplätze haben wir nacheinander modernisiert. Zunächst wurde die Fördertechnik umgebaut, anschließend neue Antriebe eingesetzt, ehe die Verdrahtung erfolgte. Dabei haben wir den dritten Kommissionierplatz zwischenzeitlich zu einer Wareneingangsstation umfunktioniert“, konkretisiert Norbert Fisch.
Dank neuer Stichstraßen können die Kommissionierpunkte heute voneinander unabhängig mit Material versorgt werden. Zudem verfügt jede Station über ausreichend Puffer. „Unser Ziel war es, dass die Mitarbeiter immer ausreichend Material zur Verfügung haben und nicht wie zuletzt darauf warten müssen. Nur so erreichen wir eine hohe Pick-Zahl“, erläutert Marcel Schwarze. „Die Erneuerung der Fördertechnik und die Umstrukturierung der Fahrwege hat bereits eine deutliche Leistungssteigerung der Anlage bewirkt“, legt Norbert Fisch dar. „Dank dieser Maßnahmen könnten wir Stand heute die Leistung des Lagers um weitere 40 Prozent steigern, bevor wir die mechanischen Kapazitätsgrenzen erreichen.“
Neues viadat sorgt für zusätzliches Leistungsplus
Der letzte Schritt der Erweiterung war schließlich das Upgrade des Lagerverwaltungssystems auf die neue Version viadat 9. „Um die Software optimal einsetzen zu können, mussten wir zunächst sämtliche Prozesse überarbeiten,“ resümiert Christian Fehlau, der als Sales Manager bei viastore für das Projekt zuständig war. viadat ist intuitiv bedienbar und bietet bereits im Standard mehr als 2.500 Funktionen.
„Besonders wichtig war uns die ABC-Kategorisierung der Lagerartikel, um die Fahrwege der Regalbediengeräte zu optimieren“, betont Lagerleiter Oliver Fuchs. „Diese ermöglicht einen schnelleren Zugriff, steigert die Pick-Zahlen und erzeugt dadurch eine höhere Kommissionierleistung.“ Zudem bietet die aktuelle Version des Lagerverwaltungssystems wesentlich bessere Auswertungsmöglichkeiten. „Bei der über 20 Jahre alten Version mussten wir unsere Auswertungen zeitaufwendig mit Excel erstellen. Mit viadat 9 erhalten wir die gewünschten Zahlen auf einem individuellen Dash-Board mit nur einem Klick“, führt Fuchs aus. „So hat man alle Entwicklungen im Blick und kann vorausschauend Einfluss nehmen. Das spart nicht nur Zeit, die Anlage wird außerdem optimal ausgelastet und die Produktion lässt sich einfacher an die Logistik anbinden“, zeigt Norbert Fisch auf.
Zeitplan übertroffen
Die Inbetriebnahme des neuen Lagers erfolgte eine Woche vor dem eigentlichen Termin. Norbert Fisch ist noch immer beeindruckt: „Dass die Koordination trotz der vielen Projektbeteiligten so gut funktioniert hat, ist schlichtweg gigantisch und veranschaulicht, warum viastore eines der führenden Unternehmen der Branche ist.“ Doch viastore hat nicht nur den Terminplan eingehalten, sondern auch das angestrebte Leistungsplus von 25 Prozent umgesetzt. Auch Werksleiter Frank Aschenbach zieht ein positives Fazit: „Obwohl wir unser Werk während der Modernisierungs- und Umbauphase in Höchstlast betrieben haben, wurde das Projekt ohne Produktionsausfall gestemmt. Das ist eine herausragende Leistung.“