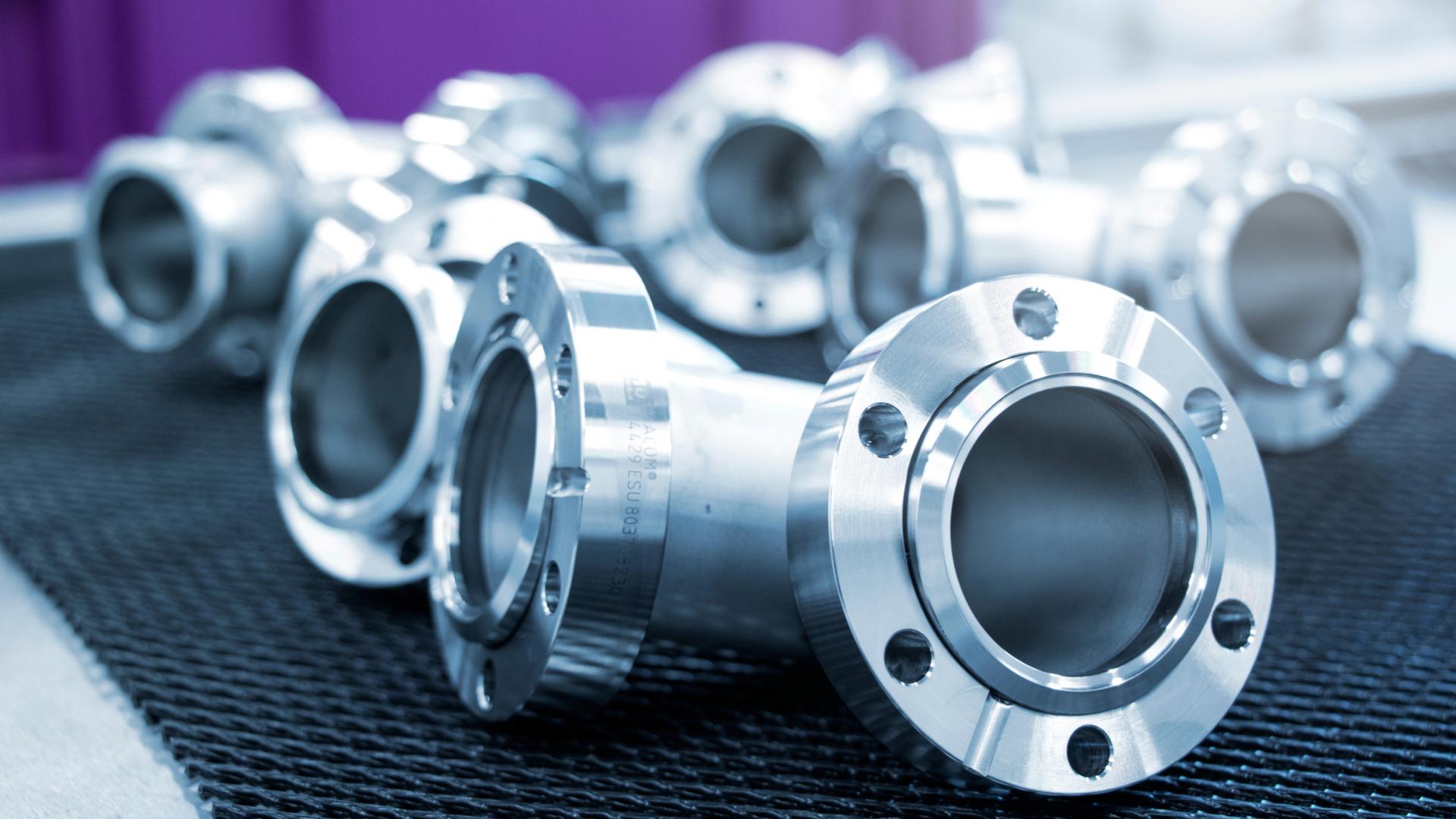
Se juntan logística y producción
"Cuanto más componentes fabricamos y más compleja es la producción, más se convirtió en un agujero negro", recuerda Kevin Mahler, COO de VACOM GmbH. La empresa creada en 1992 con sede en Jena fabrica componentes para aplicaciones en alto vacío y ultra alto vacío. Lo hace con éxito, porque la demanda de componentes de vacío ultra-limpios está creciendo en cada vez más ámbitos, como por ejemplo en la investigación, la producción de chips o para el recubrimiento de ópticas y pantallas. Sólo en el último año y medio la empresa creció por más de 100 personas. En la actualidad, VACOM tiene una plantilla de alrededor de 350 personas, tiene otras 120 vacantes y es uno de los principales proveedores europeos de tecnología de vacío.
Producción altamente compleja
El rápido crecimiento presenta nuevos desafíos a la empresa: gestionar los procesos de forma eficiente y, al mismo tiempo, mantener el control del conjunto requiere grandes esfuerzos. "Nuestros productos son sumamente complejos, algunos están compuestos por varios centenares de componentes", explica Mahler. La mayoría de estos componentes, como por ejemplo las bridas, las fabrica el propio VACOM – en tamaños de lote de hasta 1.000 unidades. "Fabricamos productos complejos, como nuestras cámaras de vacío esféricas o cilíndricas, a medida según las exigencias del cliente." En estos casos, el tamaño de lote típico está entre uno y diez como máximo – Kevin Mahler lo denomina "construcción de prototipos en serie". Durante el proceso de producción, las piezas semiacabadas se trasladan repetidamente entre los diferentes procesos y máquinas. Una fabricación clásica en línea no sería posible. Los sistemas clásicos de control de producción, como el Kanban, tampoco sirven para VACOM ya que en una estación pocas veces se requiere el mismo componente. Por ello, al comenzar el procesamiento de un pedido, los operarios de VACOM tienen que juntar todo el material requerido y luego repartirlo por las diferentes máquinas y estaciones de trabajo.
La búsqueda de material consume demasiado tiempo
"Entregábamos los productos semiacabados y materia prima a la producción y obtuvimos un producto final", describe Mahler. "Sabíamos lo que pasaba en la producción, pero no teníamos información sobre dónde exactamente se encontraban los diferentes materiales en cada momento." Por ello, para VACOM resultó difícil reaccionar a cambios. "Nuestros trabajadores gastaron cada vez más tiempo buscando componentes para transportarlos a su estación de trabajo. Al final, en cada turno había por lo menos una persona que no hacía otra cosa que buscar material", resume Kevin Mahler. Con un equipo de producción que en aquel entonces era de 50 personas esto era claramente demasiado.
Camino de la Smart Factory
Por ello, VACOM decidió convertir su producción en una "Smart Factory". A estos efectos, Mahler y su equipo primero crearon una fábrica transparente: En una representación digital definieron el recorrido de los diferentes componentes por la producción y los procesos a realizar. "Esto permite saber dónde se encuentra cada cosa, qué se está haciendo en cada momento y quién está trabajando en cada máquina", expone Kevin Mahler. Estos datos constituyeron la base para una segunda etapa en el camino hacia la fábrica inteligente – la creación de una producción con capacidad de reacción. Para ello, VACOM se apoya, por un lado, en el Manufacturing Execution System (MES) HYDRA de MPDV Mikrolab GmbH y, por el otro lado, en el Sistema de Gestión de Almacenes (SGA) viadat de viastore SOFTWARE, que ya se está utilizando para gestionar el almacén automático existente. La gestión conjunta de datos por SGA, MES y SAP ERP permite reaccionar rápidamente a exigencias modificadas o nuevas de los clientes.
En 2019 se procedió a la siguiente etapa hacia la Smart Factory: la fábrica autocontrolada. En primer lugar, Kevin Mahler tenía previsto automatizar toda la logística de producción y, por lo tanto, utilizar robots de transporte. Por ello se dirigió a viastore: "Los expertos nos explicaron que el empleo de robots de transporte formaba parte del estándar de viadat." Sin embargo, en este caso concreto, se trataba del abastecimiento logístico de la producción. Esto significa que, después de cada proceso, el SGA tiene que recibir una orden del MES para controlar los robots de forma correcta. En aquel entonces, una combinación de MES y SGA de este tipo no existió como parte de una solución estándar. Pero precisamente para permitir una integración de este tipo, viastore ya había acordado una asociación estratégica con MPDV, el proveedor de software que suministró el MES de VACOM.
Combinación de SGA y MES
En su versión actual, viadat dispone de una interfaz estándar que permite intercambiar datos con HYDRA. "A través de esta interfaz también pueden integrarse otras soluciones MES corrientes con viadat", explica Simon Kallinger quien dirigió el proyecto de VACOM para viastore. Para ello, VACOM congregó a todas las partes involucradas. Juntos definieron los detalles de cómo pueden integrar los sistemas y las competencias específicas con que deben cumplir respectivamente. El resultado fue una integración estrecha de ambos sistemas, "con SGA, MES y SAP siendo socios iguales con facultades de decisión propias", destaca Kevin Mahler. "Esto significa que MES y SGA transmiten informaciones de forma autónoma, sin que pasen por SAP." Regulan automáticamente las tareas de las aproximadamente 45 estaciones de trabajo en la producción y los seis robots de transporte.
Dos sistemas que se autoregulan
En la interacción de los sistemas, el papel de SAP queda reducido a la generación de órdenes y a entregar la orden de fabricación con la lista de piezas a HYDRA. El MES se encarga de la planificación detallada – qué máquina, herramienta, material y operario – y transmite seguidamente una lista de piezas con la correspondiente planificación a viadat. viadat, a su vez, genera órdenes de reposición para las respectivas necesidades logísticas de cada proceso que se almacenan temporalmente en el almacén de supermercado de la nave de producción. Este reduce el espacio de almacenaje temporal que se necesita en cada estación de trabajo. Poco antes del procesamiento, el SGA emite una orden de transporte y un robot transporta el material a la estación de trabajo donde se vuelve a guardar en estanterías pequeñas antes de finalmente ser procesado. Esto permite aprovechar de forma óptima las capacidades en las máquinas. El operario coloca la orden finalizada en un pulmón de salida y lo escanea. De este modo se inicia una instrucción en viadat para que un robot transporte la mercancía al almacén de supermercado o directamente a la siguiente estación de trabajo. "Es decir que viadat también entra en acción entre los diferentes pasos de procesamiento, MES y SGA comunican permanentemente" explica Kevin Mahler. Simon Kallinger añade: "Así implementamos un sistema just-in-time verdadero. viadat conoce las capacidades en los puestos de pulmón, por lo que puede planificar que se llenen continuamente y que el material esté disponible a tiempo antes de iniciar el siguiente proceso."
Se benefician los clientes y los operarios
Kevin Mahler tiene claro que la consecuencia será un aumento de la eficiencia de los operarios en las estaciones de trabajo. "Los trabajadores no tendrán que buscar el material necesario ni cargar cajas. Recibirán todo lo que necesitan para el siguiente proceso directamente en la estación. Solamente les queda preparar la máquina y procesar los materiales." De esta manera se liberan de trabajos agotadores y desagradables y se dedican exclusivamente a aquellas tareas para las cuales están formados y que les gustan. Esto, sin embargo, no solamente es válido para los operarios de las máquinas sino también para especialistas que se encargan de la organización y la ejecución de la producción. Gracias a la transparencia que resulta de la combinación de SGA y MES, saben en cada momento donde se encuentra qué material, el grado de utilización de las máquinas y el progreso del procesamiento del producto. "Su carga de trabajo se reducirá drásticamente", explica Mahler convencido. "Solamente cuando los sistemas no son capaces de resolver determinados problemas – por ejemplo, porque falta una pieza suministrada en el almacén – tiene que intervenir una persona. Los operarios ya no se utilizan para llevar cajas de un lado a otro, sino para resolver problemas."
Mejora notable de la eficiencia global
De la fabricación inteligente también se benefician los clientes de VACOM, explica Kevin Mahler: "Se optimiza el control de existencias, se reducen masivamente los tiempos de parada y de permanencia. Se aumenta nuestra capacidad y se reducen los tiempos de paso. Además, podemos servir más rápidamente a nuestros clientes." Sólo con la fábrica autocontrolada, la eficiencia general de los equipos (OEE) en la producción de VACOM se ha incrementado por entre el cinco y el diez por ciento. Kevin Mahler supone que crecerá por otros cinco a diez por ciento hasta finalizar la optimización actual y está seguro de que "solamente aquellos que son capaces de reaccionar de forma rápida y flexible a las exigencias de los clientes sin que se genere un caos tendrán éxito duradero en el mercado. En el futuro, la producción y la logística ya no podrán considerarse como dos cosas separadas."