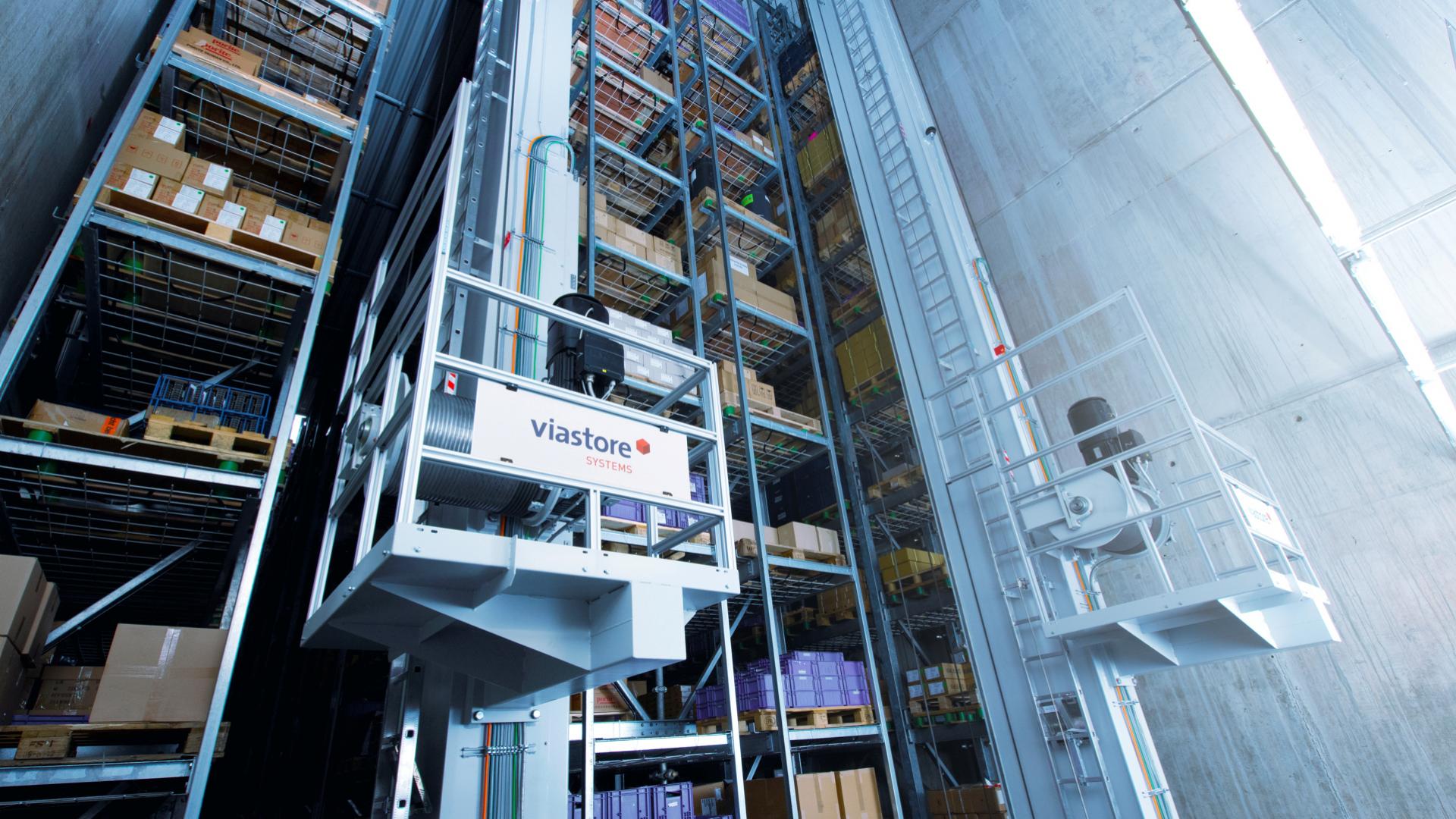
Metabo prepara su almacén de producción para el futuro
Con una buena planificación y trabajo en equipo se logra una exitosa modernización
Con numerosos componentes obsoletos era todo un desafío lograr el correcto funcionamiento del almacén de producción de Metabo en Nürtingen, Alemania, construido hace 24 años. Tras un análisis detallado de la instalación, los expertos en retrofit de viastore señalaron todos los elementos críticos y elaboraron una hoja de ruta vinculante de las medidas necesarias. Con una buena planificación previa, Metabo superó las tres semanas que duró la fase de modernización sin escasez de suministro y volvió a garantizar la disponibilidad de su almacén a largo plazo.
1995: El año en que Austria, Suecia y Finlandia ingresan en la UE, fabricantes líderes de electrónica acuerdan un estándar común para DVDs, Christo envuelve el Reichstag de Berlín. Y es el año en que Metabo, fabricante de herramientas eléctricas para usuarios profesionales, alcanza una cifra de negocios de casi 500 millones de marcos alemanes. Entonces, la empresa de Nürtingen encargó a viastore SYSTEMS, proveedor internacional de sistemas de logística interna con sede en Stuttgart, la construcción de un nuevo almacén automático para el abastecimiento de la producción a fin de crear capacidades para poder seguir creciendo.
Tras 24 años, la disponibilidad se encontraba en riesgo
Con éxito: En la actualidad, Metabo tiene una cifra de negocios de casi 500 millones de Euros – y el almacén todavía abastece el montaje de forma segura con componentes y materias primas. Sin embargo, al cabo de 24 años ya no era tan fiable. Dennis Bosch, Director de Logística de la fábrica principal, explica: "En 2005 ya habíamos modernizado el ordenador de control del flujo de materiales, sin embargo, con los años el número de errores siguió creciendo, aunque aún no era excesivo." Metabo quería evitar el riesgo de una parada, porque el almacén siempre tiene que estar disponible. Es que para la producción del fabricante de herramientas es imprescindible que las reposiciones lleguen al lugar de montaje en un plazo máximo de cuatro horas. "viastore nos recordaba periódicamente que unos componentes obsoletos de nuestra instalación suponían un riesgo para la disponibilidad", explica Bosch.
Un análisis de la instalación como base
Finalmente, en 2018, se tomó la decisión de aumentar y garantizar, para los próximos años, la disponibilidad del almacén y la fiabilidad funcional. "Para ello, viastore realizó un análisis exhaustivo de todo el sistema", dice Dennis Bosch. Lars Breuer, Director Adjunto de Retrofit de viastore, explica: "Precisamente debido a que las instalaciones logísticas son cada vez más complejas, un análisis es sumamente importante." Los expertos en retrofit examinan el estado de cada uno de los componentes y módulos del sistema de almacén. El análisis de una instalación puede durar hasta tres semanas, pero vale la pena porque como resultado se le entrega al operador un resumen gráfico que evalúa cada componente con respecto a la necesidad de su modernización representada mediante un semáforo: Si el semáforo está en "verde" no hay necesidad de actuar, el color "amarillo" significa que hay que vigilarlo y "rojo" requiere medidas urgentes. "Con este análisis identificamos muy claramente los riesgos y podemos derivar las actuaciones correspondientes. Además, elaboramos propuestas para la reorganización, ya que a menudo los procesos de nuestros clientes cambian a través de los años", ilustra Breuer.
Todo en rojo
"Tuvimos muy pocos semáforos en verde", recuerda Dennis Bosch. Lars Breuer entra en detalle: "un gran número de componentes estaban obsoletos. Piezas de recambio, sobre todo para los antiguos controles S5 en los transportadores y transelevadores, ya no estaban disponibles." Pero ante todo el hardware informático estaba obsoleto. Entre otros, para la comunicación con el sistema de transportadores todavía se utilizaba el antiguo sistema de bus Sinec L2 FMS. Las correspondientes tarjetas de interfaz de red ya no se comercializaban. "Fue el ciberataque del 2017 que nos abrió los ojos", recuerda Dennis Bosch. En aquel entonces, el virus Petya infectó a más de 1.000 estaciones de trabajo y 350 servidores de Metabo causando una interrupción de la producción y del suministro que duró varios días. Todos los sistemas afectados tenían que restablecerse completamente – con gran dificultad logramos encontrar las tarjetas de interfaz de red ya discontinuadas. "Esto nos volvió a mostrar claramente qué es lo que significa disponibilidad", destaca Bosch.
Planificación previa exacta basada en una hoja de ruta detallada
A base del análisis de la instalación, la empresa tomó la decisión de no solamente modernizar componentes individuales sino de llevar a cabo una modernización integral. "Los trabajos preparatorios necesarios fueron considerables", recuerda Dennis Bosch. "Tuvimos que extraer los artículos del almacén que se necesitaban en la producción durante el período de modernización y ubicarlos en otros lugares de la fábrica, en una carpa especialmente montada para ello, pero también directamente en los diferentes departamentos." Para que Metabo pudiera planificar esta operación, viastore presentó, además del análisis de la instalación, un marco temporal que la empresa necesitaría para realizar el retrofit. En una hoja de ruta se estableció de forma detallada en qué momento se realizaría cada trabajo. "Así sabíamos exactamente cuándo y durante cuánto tiempo estaría parada la instalación", explica Bosch. "Además sabíamos los artículos y la cantidad de los mismos que tenían que ser guardados fuera del almacén y qué teníamos que hacer en cada momento." Esto también nos ayudó en la coordinación con otros actores implicados en la empresa, por ejemplo con los departamentos donde tuvimos que liberar espacios para el almacenaje temporal de los artículos requeridos. "Fue impresionante que viastore cumplió casi al 100 por ciento la hoja de ruta ", destaca Dennis Bosch.
Totalmente modernizado en tres semanas
Durante las tres semanas anteriores a Semana Santa de 2019, el sistema logístico se modernizó a fondo: Los antiguos controles S5 se sustituyeron por modernos S7, el carro de transfer que conecta los pasillos de salida de los transelevadores (SRM) con las estaciones de picking se dotó con un nuevo accionamiento. También se modernizaron los sistemas de control y accionamientos de las tres puertas cortafuego que, en caso de incendio, separan el área de estanterías de la cabecera y el resto de la nave. "Aquí estaba instalado un sistema de control propio del fabricante que entre tanto también fue discontinuado", explica Gregor Rentschler, el Director de Proyecto de viastore responsable on site para el retrofit. "Con los nuevos sistemas de control realizamos el control de liberación inclusive alimentación eléctrica de emergencia. De este modo se garantiza que en caso de incendio se libere la línea de transportadores en las puertas cortafuego y que puedan cerrarse con seguridad." Es un aspecto que hoy día exigen los seguros contra incendios.
También se reformó el control del flujo de materiales: Ya no está concebido como hardware, sino que se ejecuta en un servidor virtual que se encuentra en un ordenador central con las correspondientes garantías de seguridad. El sistema de visualización también fue actualizado. Se modernizaron los transelevadores y los transportadores conectándolos con el sistema de bus actual. Finalmente, el control S7 de los transportadores está conectado mediante Ethernet con sistemas superiores, de modo que a partir de ahora se puede realizar el mantenimiento de la instalación y de cada uno de sus componentes de forma remota.
Un 30 por ciento más de rendimiento por la sustitución de los transelevadores
La medida más espectacular fue la sustitución de los transelevadores antiguos. "Sabíamos que nuestro carro de transfer todavía tenía reservas de rendimiento", explica Dennis Bosch. "Por ello, con el reequipamiento queríamos a la vez también aumentar el rendimiento de los transelevadores." Entonces, viastore calculó las mejoras de rendimiento que resultarían de la sustitución de los transelevadores por modelos actuales en comparación con la mera modernización de los dispositivos antiguos, y también los costes adicionales que esto supondría. "Con transelevadores dinámicos completamente nuevos logramos un aumento del rendimiento del 30 por ciento", relata Lars Breuer. Así que la decisión fue fácil. Los dos dispositivos antiguos y los carriles de traslación se retiraron a través de dos aperturas en la cubierta y por las mismas se introdujeron los transelevadores nuevos.
Trabajo en equipo que funciona
El cuerpo de bomberos de la empresa se encargó de la seguridad en la cubierta y además ayudó en la retirada e introducción de los mástiles. "El hecho de realizar este proyecto junto con el personal de Metabo hizo que el trabajo fue algo especial", destaca Gregor Rentschler. Un reflejo de esta buena sintonía fue, entre otros, el pastel casero que trajo Dennis Bosch a la obra. "La comida era de primera", admite Gregor Rentschler sonriendo y vuelve a destacar: "Para realizar un proyecto de esta índole es importante que funcione la interacción entre nuestros expertos y el personal del cliente." Dennis Bosch afirma, "que el equipo fue clave para la realización exitosa de todo el proyecto." Por ello, para él es importante que se mencionen por sus nombres los integrantes del equipo central de Metabo: "Me quito el sombrero ante Uwe Hennig, Mike Kießig, Steffen Killer, Martin Lehr, Tobias Fuchs, Kevin Rebelo y todo el equipo de logística. Todos ellos han hecho un trabajo excelente. También los demás colaboradores y áreas implicadas en los trabajos previos y posteriores hicieron un gran trabajo, un gran esfuerzo de equipo."
Un aumento de rendimiento del almacén
Hace pocos meses que la instalación modernizada está en funcionamiento, pero ya se notan los éxitos: "Todavía es muy temprano para dar cifras concretas.", explica Dennis Bosch. "Pero sé que el rendimiento crecerá, como prometido, en una magnitud de dos dígitos. Los operarios en el almacén ya constataron que el sistema es más rápido. No solamente se extraen más rápidamente las mercancías, ahora también los registros de datos están disponibles de inmediato." Con el mantenimiento remoto es posible rápidamente corregir incidencias online. Además, se reducirá el consumo de energía porque en los nuevos transelevadores el acoplamiento por el circuito intermedio se encarga de la compensación interna de energía de las cargas motrices y generadoras. "Todo el proyecto de modernización se desarrolló muy bien", resume Dennis Bosch con satisfacción. Recomienda que las empresas que tienen previsto modernizar su instalación "se tomen el tiempo suficiente para la planificación previa. Esto no se debe subestimar. El análisis de la instalación y la hoja de ruta detallada de viastore son una base fiable para ello."