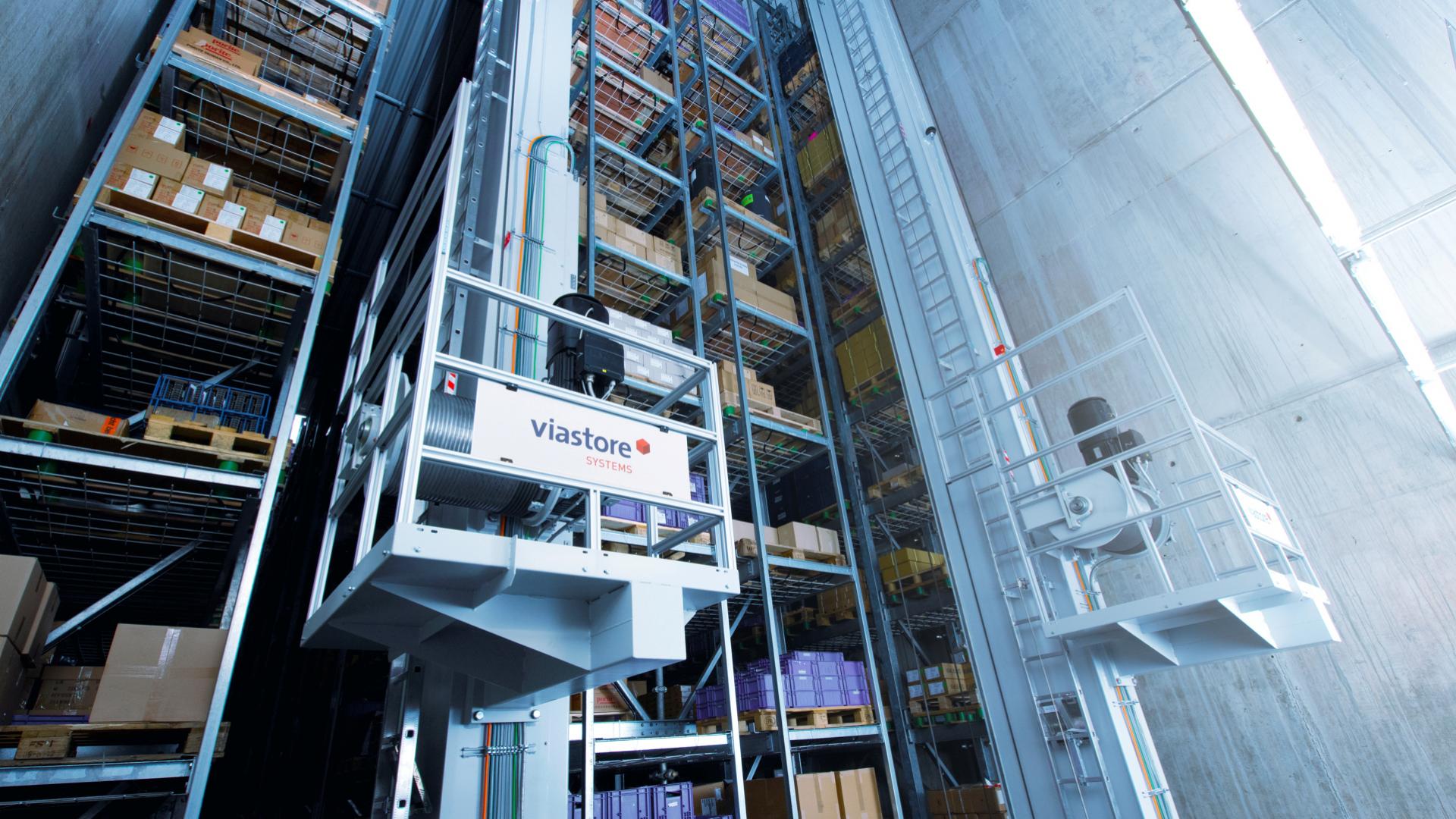
Metabo Makes Production Warehouse future-proof
With Good Planning and Teamwork for a Successful Retrofit
Many components were discontinued. This was a challenge for the smooth operation of Metabo’s 24-year-old production warehouse in Nürtingen (Southern Germany). With a detailed system analysis, the viastore retrofit experts identified all critical elements and created a binding roadmap for the measures required. Thus, with good advanced planning, Metabo was able to manage the three-week modernization phase without any supply bottlenecks and ensure long-term availability of the warehouse.
1995: The year in which Austria, Sweden and Finland joined the EU, leading electronics manufacturers agreed on a common standard for DVDs, and Christo wrapped the Reichstag in Berlin. And in which Metabo, a traditional manufacturer of power tools for professional users, is increasing its turnover to almost half a billion Deutschmarks. At that time, the company based in Nürtingen (near Stuttgart) had viastore SYSTEMS, the Stuttgart-based international supplier of intralogistics systems, build a new automated warehouse to provide supplies to production in order to create capacity for further growth.
After 24 years a risk for availability
With success: Today Metabo scratches the 500 million turnover mark – and the warehouse still supplies production safely with components and raw materials. However, after 24 years, reliability was no longer entirely adequate, as Dennis Bosch, Head of Logistics at the main plant, explains: "Although we had modernized the material flow computer back in 2005, the number of failures increased over the years, even if it was not proliferating." Metabo wanted to avoid the risk of a shutdown, because the warehouse must always be available – production at the tool manufacturer is structured in such a way that replenishment must be available at the production site after a maximum of four hours. "viastore has regularly reminded us that obsolete components pose a risk to availability in our plant," says Bosch.
System analysis as the basis
Finally, in 2018, the decision was made to increase the availability and reliability of the warehouse, and secure it for the next few years. "For this, viastore extensively analyzed the condition of the entire system", says Dennis Bosch. Lars Breuer, Assistant Director Retrofit at viastore, explains: "Because logistics systems are becoming increasingly complex, an analysis is extremely important." The retrofit experts examine the condition of each component and each module of the warehouse system. Such a system analysis can take up to three weeks – but the effort is well worth it. As a result, the operating company receives a graphical overview, which evaluates each component in terms of its modernization needs and displays it in the form of a traffic light: If the traffic light is "green", there is no need for action, "yellow" issues should be kept in mind, and "red" requires the fastest possible measures. "With this analysis, we work out the risks very clearly and can derive corresponding actions. In addition, we develop proposals for reorganization, as our customers' processes often change over the years," explains Breuer.
All traffic lights on red
"There was hardly a traffic light on green", Dennis Bosch remembers. Lars Breuer goes into detail: "Many components were discontinued. Spare parts were no longer available for the old S5 controls in the conveyor system and the automated storage and retrieval systems." Above all, the IT hardware was outdated. It relied on the old Sinec L2 FMS bus system for communication with the conveyor system, for which the interface cards were no longer available. "It was the cyber attack of 2017 that opened our eyes permanently," recalls Dennis Bosch. At that time, the virus Petya infected more than 1,000 workstation computers and 350 servers at Metabo and caused an interruption of production and supply lasting several days. All affected systems had to be completely rebuilt – the discontinued interface cards could only be organized with difficulty somewhere else. "That made it clear once again what availability means," says Bosch.
Exact planning based on a detailed roadmap
Based on the system analysis, the company decided not only to modernize individual components, but to carry out a comprehensive retrofit. "The necessary preparatory work was quite extensive," recalls Dennis Bosch. "We had to remove material from the warehouse that was needed in production during the period of modernization, and put them in other places in the factory – in a specially built tent and also directly in the various departments." To allow Metabo to schedule of all this, viastore defined a time frame that the company would need for the retrofit. A roadmap detailed what work would be done, and when. "So we knew exactly when and how long the plant would stand still," explains Bosch. "In addition, we were able to say which and how many parts from the warehouse we had to accommodate externally and what we had to do at what time." This also helped with the coordination with all other involved parties in the company, for example those departments in which we had to make room for the temporary storage of the required parts. "It was impressive that viastore adhered to the roadmap almost 100 percent," emphasizes Dennis Bosch.
Completely modernized in three weeks
In the three weeks leading up to Easter 2019, the logistics system was completely modernized: The old S5 controls were replaced by modern S7, and the shuttle car – which connects the outbound aisles of the storage and retrieval machines with the pick stations – was given a new drive. The controls and drives of the three fire protection doors, which separate the rack area from the pre-zone and the rest of the hall in case of fire, were also modernized. "There was a separate control installed by the manufacturer, which had also been discontinued," explains Gregor Rentschler, the viastore project manager who was responsible for the retrofit on site. "With the new controls, we have implemented a gate clearance control including emergency power supply – this ensures that the conveyor line at the fire doors is cleared in the event of a fire and the doors can close safely." This is an aspect demanded by fire insurance companies today.
The material flow computer has also been redesigned: It is no longer running as hardware, but runs on a virtual server, which is located on a mainframe and is backed up accordingly. The visualization has also been updated. The storage and retrieval machines and the conveyor system were updated to a current bus system. And the S7 control of the conveyor system is connected to superordinate systems via Ethernet, so that remote maintenance for the system is possible right down to each individual component.
Replacing the AS/RS increased the performance by 30 percent
The most spectacular measure was the replacement of the old storage and retrieval machines. "We knew that our shuttle car still had power reserves," explains Dennis Bosch. "So we also wanted to increase the performance of the storage and retrieval machines." viastore then calculated what increase in performance would be achieved by the replacement of the AS/RS by current models in comparison to a mere modernization of the old machines – and what would be the extra costs. "With completely new, more dynamic AS/RS, we achieve a performance increase of 30 percent," says Lars Breuer. So the decision was easy. The two old machines and the floor crane rails were removed through two hatches in the roof, and the new ones were installed in the same way.
Good teamwork
The company fire brigade took care of securing the work on the roof and also helped with removing and installing the masts. "Handling the project together with the Metabo employees made the work particularly special", emphasizes Gregor Rentschler. A sign of this good cooperation was the home-baked cake that Dennis Bosch brought to the construction site. "The food was great", Gregor Rentschler admits with a smile and emphasizes once again: "It is important that in such a project, the interaction of our experts and the customer's employees works." Dennis Bosch confirms that "the team was key to successfully implementing the overall project." It is therefore important to him that his Metabo core team be mentioned by name: "I take my hat off to Uwe Hennig, Mike Kießig, Steffen Killer, Martin Lehr, Tobias Fuchs, Kevin Rebelo and the entire logistics team. They all have done a great job. And the other colleagues and departments involved in the preparation and follow-up also did a great job – a great team effort."
A performance boost for the warehouse
Although the modernized plant has only been in operation for a few months, there is already some success: "It is still too early to give specific figures," reports Dennis Bosch. "But I assume that the increase in performance will result in the promised double-digit range. The colleagues in the warehouse have already noticed that the system is running faster. Not only is the material outside faster, but the data records are also available fast as lightning." Remote maintenance allows events to be resolved online very quickly. In addition, the energy consumption will decrease because in the new AS/RS, a DC link coupling ensures the internal energy compensation of motoric and regenerative loads. "The entire retrofit project went very well," says Dennis Bosch happily. He recommends that companies that intend to modernize their plant "have enough time for pre-planning – that should not be underestimated. The system analysis and the detailed roadmap from viastore are a reliable basis."