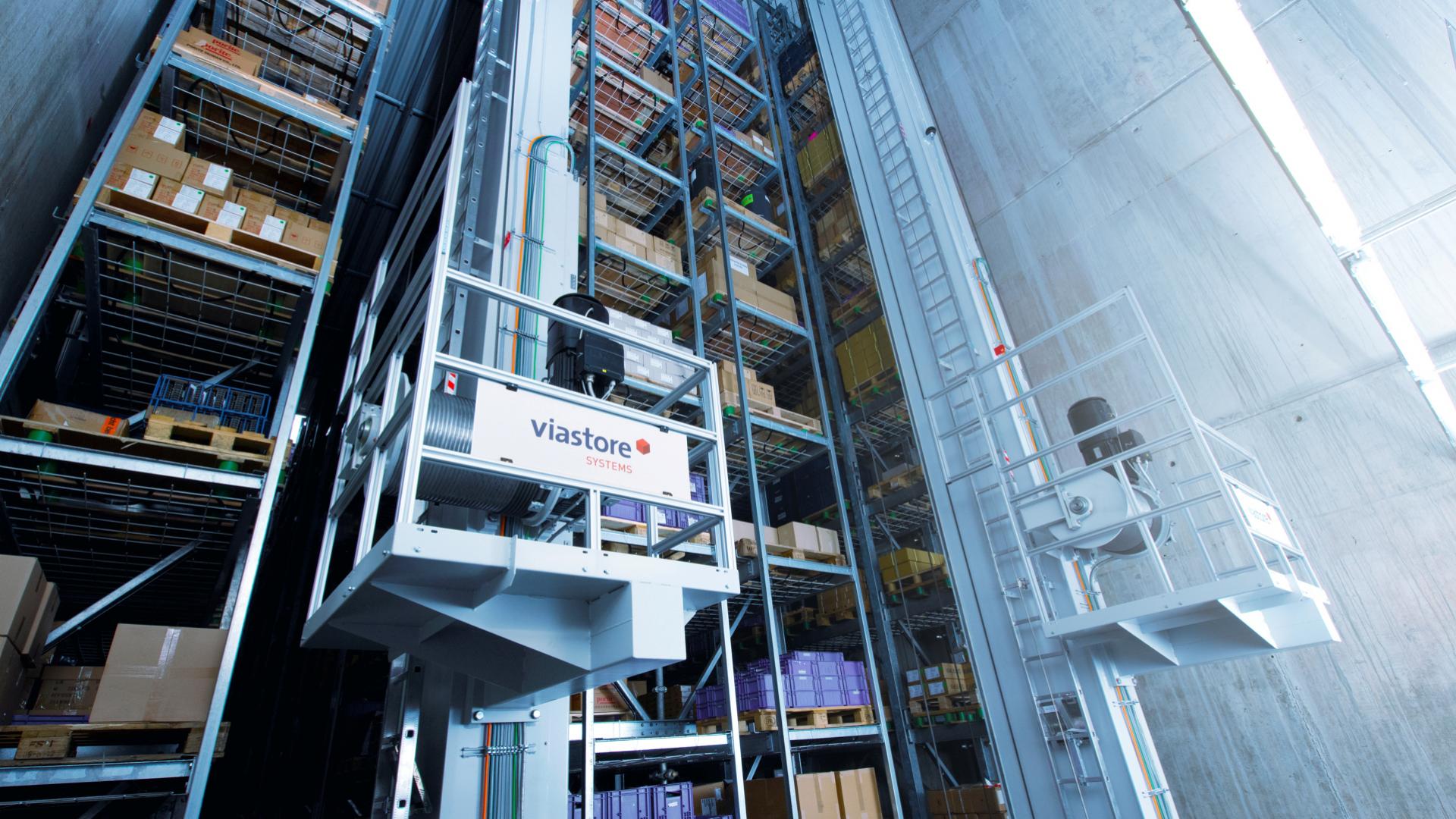
Metabo garantit la pérennité de son entrepôt de production
Avec une bonne planification et un travail d'équipe pour une mise à niveau réussie
De nombreux composants étaient devenus obsolètes. C'était un défi pour le bon fonctionnement de l'entrepôt de production de Metabo, vieux de 24 ans, à Nürtingen (Allemagne). S'appuyant sur une analyse détaillée de l'installation, les spécialistes Retrofit de viastore ont présenté tous les éléments critiques et ont établi une feuille de route contraignante pour les mesures nécessaires. Grâce à une bonne planification, Metabo a pu surmonter les trois semaines qu'a duré la phase de modernisation sans pénurie d'approvisionnement et garantir à nouveau la disponibilité de l'entrepôt sur le long terme.
1995 : l'année durant laquelle l'Autriche, la Suède et la Finlande ont adhéré à l'UE, les principaux fabricants d'électronique se sont mis d'accord sur une norme commune pour les DVD et Christo a enveloppé le Reichstag à Berlin. Et pour Metabo, fabricant traditionnel d'outils électriques à l'usage des professionnels, ce fut l'année au cours de laquelle son chiffre d'affaires a grimpé jusqu'à atteindre près d'un demi-milliard de marks. À l'époque, l'entreprise de Nürtingen avait fait construire, pour l'approvisionnement de sa production, un nouvel entrepôt automatisé par le fournisseur international de systèmes intralogistiques viastore SYSTEMS, basé à Stuttgart, afin de créer les capacités nécessaires à sa future croissance.
24 ans après, la disponibilité est en péril
Avec succès : le chiffre d'affaires de Metabo flirte aujourd'hui avec la barre des 500 millions d'euros, et l'entrepôt assure toujours en toute fiabilité l'approvisionnement de l'atelier de montage en composants et en matières premières. Pourtant, 24 ans plus tard, la fiabilité n'était plus entièrement assurée, comme l'explique Dennis Bosch, responsable de la logistique à l'usine principale : « Nous avions déjà modernisé l'ordinateur du flux de marchandises en 2005, mais le nombre d'anomalies a augmenté au fil des ans, même s'il n'a pas dégénéré ». Metabo voulait écarter tout risque d'immobilisation, car l'entrepôt doit être disponible à tout moment. La production chez le fabricant d'outils est en effet structurée de telle manière que le réapprovisionnement doit être présent sur le site de montage dans un délai de quatre heures maximum. « viastore nous a régulièrement rappelé que les composants obsolètes de notre installation représentaient un risque pour la disponibilité », explique M. Bosch.
L'analyse de l'installation comme point de départ
En 2018, il a finalement été décidé de renforcer la disponibilité et la fiabilité de l'entrepôt et de garantir sa pérennité pour les années à venir. « Dans cette perspective, viastore a procédé à une analyse approfondie de l'état de l'ensemble de l'installation », déclare Dennis Bosch. Lars Breuer, responsable adjoint Retrofit chez viastore, explique : « C'est précisément parce que les installations logistiques deviennent de plus en plus complexes qu'une analyse est extrêmement importante ». Les spécialistes Retrofit inspectent l'état du moindre composant du système de stockage. Une telle analyse peut prendre jusqu'à trois semaines, mais le jeu en vaut la chandelle. Car, en guise de conclusion, l'exploitant reçoit une présentation graphique qui évalue chaque composant quant à ses besoins de modernisation et les identifie sous la forme d'un feu de signalisation : un feu « vert » indique qu'aucune démarche n'est requise , un feu « jaune », que le composant est à surveiller et un feu « rouge », que des mesures d'urgence sont nécessaires. « Cette analyse nous permet d'identifier très clairement les risques et d'en déduire les démarches à effectuer. Nous élaborons également des propositions de réorganisation car les processus de nos clients varient énormément au fil des années », explique M. Breuer.
Tout en rouge
« Nous n'avons obtenu aucun feu vert », se souvient Dennis Bosch. Lars Breuer entre dans les détails : « De très nombreux composants étaient devenus obsolètes. Il n'y avait plus de pièces de rechange disponibles pour les anciens automates de la série S5 du système de manutention et des transstockeurs. « Mais c'était surtout l'équipement informatique qui était dépassé. Pour la communication avec le système de manutention, il utilisait encore l'ancien système de bus Sinec L2 FMS pour lequel il n'existait plus de carte d'interface. « La cyberattaque que nous avons subie en 2017 nous a durablement ouvert les yeux », se souvient Dennis Bosch. À l'époque, le virus Petya avait infecté plus de 1 000 postes de travail, ainsi que 350 serveurs chez Metabo, provoquant une interruption de la production et des livraisons pendant plusieurs jours. Tous les systèmes concernés ont dû être entièrement réinstallés, et il n'a été possible de se procurer les cartes d'interface déjà obsolètes qu'avec beaucoup de peine. « Cela nous a une nouvelle fois montré clairement ce que signifiait la disponibilité », souligne Dennis Bosch.
Planification précise sur la base d'une feuille de route détaillée
En se fondant sur l'analyse de l'installation, l'entreprise a décidé de ne pas seulement moderniser les différents composants, mais aussi de procéder à une transformation globale. « Les travaux préparatoires nécessaires ne furent pas de tout repos », se rappelle Dennis Bosch. « Car nous avons dû sortir de l'entrepôt les articles qui étaient requis pour la production pendant la phase de modernisation et les placer dans d'autres endroits de l'usine – sous un chapiteau érigé tout spécialement, mais aussi directement dans les différents départements. Pour que Metabo puisse planifier l'opération, viastore a établi, parallèlement à l'analyse de l'installation, un planning dont l'entreprise aurait besoin pour la transformation. Une feuille de route décrivait de manière détaillée les travaux à effectuer et à quel moment. « Ainsi, nous savions précisément quand et combien de temps l'installation serait à l'arrêt », explique Dennis Bosch. « En outre, nous étions capables de dire quels articles de l'entrepôt nous devions stocker en externe et dans quelle quantité, et ce que nous avions à faire et à quel moment ». Cela nous a également aidé à coordonner les travaux avec tous les autres acteurs de l'entreprise, par exemple avec les services dans lesquels nous devions faire de la place pour le stockage temporaire des articles requis. « Il est frappant de constater que viastore a respecté la feuille de route à presque 100 pour cent », souligne Dennis Bosch.
Modernisation complète en trois semaines
Les trois semaines qui ont précédé Pâques 2019 furent consacrées à la modernisation de fond en comble de l'installation logistique : les anciens automates S5 ont été remplacés par des automates S7 modernes, tandis que le chariot de transfert, qui relie les allées des transstockeurs (TK) et les postes de préparation des commandes, a reçu un nouvel entraînement. Les automates et les entraînements des trois portes coupe-feu qui séparent les rayonnages de la zone de préparation et le reste du bâtiment en cas d'incendie, ont également été modernisés. « Le fabricant avait installé ici son propre automate qui était également devenue obsolète », explique Gregor Rentschler, qui, en tant que chef de projet chez viastore, était responsable de la transformation du site. « Grâce aux nouveaux automates, nous avons réalisé une automatisme de dégagement avec alimentation électrique de secours, ce qui garantit qu'en cas d’incendie, le parcours est dégagé au niveau des portes coupe-feu et les portes peuvent se fermer en toute sécurité ». Une exigence actuelle des assurances contre l'incendie.
L'ordinateur du flux des marchandises a également été repensé : il n'est plus conçu comme un équipement informatique physique, mais fonctionne sur un serveur virtuel qui se trouve sur un ordinateur central et qui est sécurisé en conséquence. La visualisation a aussi bénéficié d'une mise à jour. Les transstockeurs et le système de manutention ont été modernisés avec un système de bus actuel. L’automate S7 du système de manutention a ensuite été raccordée via Ethernet aux systèmes hiérarchiquement supérieurs, de sorte qu'il est désormais possible d'effectuer une maintenance à distance de l'installation jusqu'au moindre composant.
Le remplacement des TK a apporté 30% de productivité supplémentaire
La mesure la plus spectaculaire fut le remplacement des anciens transstockeurs. « Nous savions que notre chariot de transfert avait encore des réserves de performance », explique Dennis Bosch. « Dans le cadre de la modernisation, nous voulions donc également augmenter la productivité des transstockeurs ». viastore a alors calculé ce que le remplacement des transstockeurs par des modèles actuels apporterait en termes de gain de productivité par rapport à une simple modernisation des anciens transstockeurs – et le surcoût que cela engendrerait. « Avec des transstockeurs entièrement neufs et plus dynamiques, nous obtiendrions une augmentation de la productivité de 30 pour cent », explique Lars Breuer. À partir de là, la décision fut facile à prendre. Les deux anciens transstockeurs ainsi que les rails de roulement ont été sortis par deux lucarnes du toit et les nouveaux transstockeurs ont été introduits de la même façon.
Un travail d'équipe payant
Les pompiers de l'entreprise se sont occupés de la sécurité sur le toit et ont par ailleurs apporté leur aide pour l'introduction et l'évacuation des mâts. « La gestion du projet en collaboration avec les employés de Metabo a rendu ce travail particulier », souligne Gregor Rentschler. Un signe de cette bonne collaboration est notamment le gâteau que Dennis Bosch a apporté sur le chantier. « La nourriture était excellente », reconnaît Gregor Rentschler dans un sourire, avant de souligner : « Pour une opération de ce genre, il est important que la collaboration fonctionne bien avec nos experts et les salariés du client ». Dennis Bosch confirme « que l'équipe a été la clé de la réussite du projet global ». Il est donc important pour lui de mentionner nommément chacun des membres de son équipe principale chez Metabo : « Je salue Uwe Hennig, Mike Kießig, Steffen Killer, Martin Lehr, Tobias Fuchs, Kevin Rebelo et l'ensemble de l'équipe logistique. Ils ont tous fait un travail formidable. Les autres collègues et secteurs impliqués dans la préparation et le suivi du projet ont également accompli des prouesses – une super performance collective ! ».
Gain de performance pour l'entrepôt
Bien que l'installation modernisée ne soit en service que depuis quelques mois, des succès se profilent déjà : « Il est encore trop tôt pour donner des chiffres concrets », explique Dennis Bosch. « Mais je ne doute pas que l'amélioration des performances se situera sur la fourchette à deux chiffres promise. Les collègues de l'entrepôt ont déjà constaté que l'installation fonctionne plus rapidement. Les marchandises sortent plus rapidement et les données sont désormais disponibles en un éclair ». Grâce à la télémaintenance, les incidents peuvent être réglés plus rapidement en ligne. En outre, la consommation d'énergie va baisser car, dans les nouveaux TK, un couplage de circuit intermédiaire assure une compensation d'énergie interne entre les charges des moteurs et des générateurs. « L'ensemble du projet de modernisation s'est très bien passé », résume Dennis Bosch avec satisfaction. Aux entreprises qui envisagent une modernisation de leur installation, il recommande de « prendre suffisamment de temps pour la planification, qu'il ne faut pas sous-estimer. L'analyse de l'installation et la feuille de route détaillée de viastore constituent à cet égard une base fiable ».