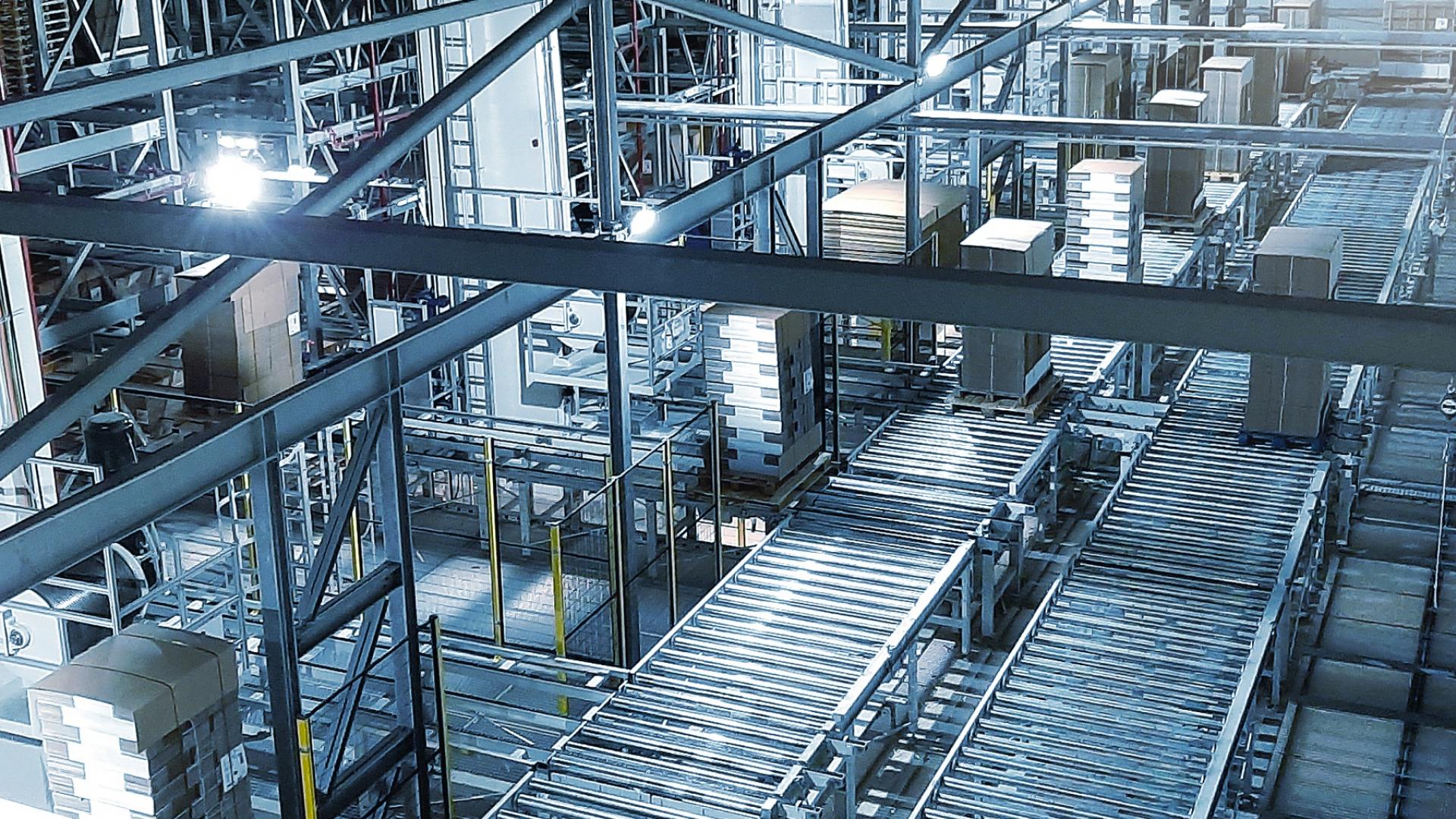
Un projet sans précédent dans l'industrie française du carton ondulé
Des coûts élevés dus à la location d'espaces de stockage externes, des dommages pendant les transports, des processus compliqués dans la chaîne d'approvisionnement et le désir d’améliorer l’impact environnemental. Voici les raisons qui ont incité VPK France à construire un magasin automatisé à hauts rayonnages de 6 000 mètres carrés à côté de son site de production à Saint-Quentin dans les Hauts-de-France. Fondée en 1935, cette entreprise familiale propose une large gamme de solutions sur mesure pour les emballages en carton ondulé et carton compact, les mandrins et les cornières.
Le carton ondulé, un produit aux multiples défis
VPK fabrique du carton ondulé à Saint-Quentin, un produit qui prend beaucoup de place pour une valeur comparativement faible en raison de sa nature et du grand nombre de formats différents. En conséquence, les problèmes liés à la conception des entrepôts et aux processus de travail ne sont pas rares. Le stockage du carton ondulé génère des coûts élevés surtout si, comme c'est le cas pour VPK, il est effectué via un espace externe loué. En effet, il faut toujours des moyens de transport supplémentaires tels que des camions ou des chariots élévateurs pour transporter le produit de l'usine à l'entrepôt. Cela a eu des effets négatifs non seulement sur la chaîne d'approvisionnement, mais aussi sur l'environnement; une question majeure pour le groupe VPK, qui est fortement engagé dans le développement durable.
Une décision mûrement réfléchie
Afin de ne plus dépendre d'un espace de stockage externe, VPK a décidé d'agrandir son site de production avec un magasin automatisé à hauts rayonnages. L'entreprise souhaitait ainsi créer davantage de capacités de stockage, éviter les goulets d'étranglement et offrir à ses clients une qualité maximale. VPK ont rapidement trouvé le partenaire idéal pour le projet : La filiale française de l'expert en intralogistique viastore, qui est basée à Saint-Jean-de-Braye près d'Orléans. En tant qu'entrepreneur général avec plus de 50 ans d'expérience, viastore offre un savoir-faire complet en matière de processus, une technologie système de pointe et, avec son logiciel de gestion d'entrepôt viadat (WMS), une solution logicielle de pointe pour les flux de matériaux en réseau et automatisés.
VPK en était persuadé : seul un magasin automatisé peut garantir une transparence dynamique et permanente de tous les niveaux de stock ainsi que la haute qualité du produit. "Statistiquement, la cause première de non-qualité du carton ondulé vient des coups de fourche et des chocs lors de la manutention. Tout cela n’existe plus avec notre système automatisé, puisque nous n’avons plus aucune rupture de charge jusqu’au camion.", déclare Philippe Tran, directeur général de VPK France, en expliquant les avantages du magasin à hauts rayonnages automatisé.
La production et le stockage deviennent voisins
Pour VPK, viastore a mis en place un magasin grande hauteur à double profondeur et à six allées, qui peut accueillir jusqu'à 25 000 palettes sur une surface totale de 6 000 mètres carrés et mesurant 37 mètres de hauteur, ce qui est une taille d'entrepôt jamais vue en France dans le secteur du carton ondulé.
Grâce à sa connexion directe avec l'usine, le magasin peut directement absorber le flux de production interne. Les produits finis et semi-finis sont stockés. Plus de 40 types de palettes différents sont utilisés chez VPK, dont la palette Euro. En raison de ce grand nombre de référence, une étape intermédiaire est nécessaire avant le stockage des palettes clients : avant que les palettes clients ne soient stockées, un robot portique les place sur des palettes esclaves afin de standardiser les différents formats. Ensuite, les six transstockeurs, qui sont optimisés pour les différentes tailles de palettes, saisissent les palettes de manière entièrement automatisée.
Pour les marchandises sortantes, les palettes sont transportées vers deux zones de préparation via le système de convoyage automatique. Là, deux robots séparent les différentes palettes clients de la palette esclave avant qu'elles ne soient distribuées aux huit différentes rampes de chargement de la zone d'expédition. La particularité est que la préparation des commandes est basée sur une séquence calculée par des algorithmes. Les palettes sont prélevées dans l'ordre exact où elles sont nécessaires, puis préparées sur des convoyeurs au sol encastrés pour simuler le chargement d'un camion. Dès que le chargement est complet, il est transporté par le convoyeur au sol jusqu'au cariste, qui n'a plus qu'à charger les palettes dans le camion dans le bon ordre selon le principe de "Marchandises vers l’homme" (Goods to man). Des photos sont automatiquement prises pendant le processus de chargement pour illustrer que celui-ci s'est déroulé sans incident.
viadat WMS contrôle les processus et gère le magasin
Les articles dans l'entrepôt ainsi que tous les mouvements et la répartition des tâches sont gérés et contrôlés par le logiciel de gestion d'entrepôt (WMS) viadat. Ce logiciel de gestion d'entrepôt intuitif a été développé par viastore SOFTWARE GmbH, une filiale de viastore SYSTEMS, et est déjà doté de plus de 2 500 fonctions logistiques en standard, qui peuvent être étendues et adaptées aux besoins spécifiques des clients. Les principales tâches de viadat dans le magasin de VPK sont le contrôle des entrées et sorties de produits finis et semi-finis et la gestion des palettes esclaves entrantes et sortantes. Sur la base des ordres de livraison entrants, le système organise un contrôle continu des palettes en temps réel selon le principe FIFO (First in - First out). Cela signifie que plus la date de livraison d’une palette approche, plus elle est placée en avant dans le rayonnage. Ce principe est extrêmement difficile à mettre en œuvre dans un magasin manuel ou à l'aide d'un chariot élévateur.
En outre, viadat prend en charge l'empilage des palettes vides des clients et leur retour. Les retours des clients sont également traités par le logiciel de gestion d’entrepôt. Grâce à son interface standard, viadat est toujours en échange étroit avec le système ERP GesPack, que VPK utilise.
Augmentation des capacités de stockage, amélioration de l'empreinte carbone
Dès la mise en service de l'entrepôt grande hauteur, les avantages deviennent évidents : l'automatisation évite d'endommager le produit, la palettisation est de meilleure qualité et les palettes individuelles peuvent être identifiées avec plus de précision. "viadat permet une transparence nettement supérieure. Les employés savent à tout moment où se trouve chaque palette. Toute la chaîne logistique de VPK est désormais beaucoup plus fiable et efficace qu'auparavant", résume Frédéric Juillet, chef de projet informatique de viastore SYSTEMS, qui est responsable du projet.
VPK réalise des économies à long terme en démantelant progressivement les zones de stockage externe. En outre, le magasin à hauts rayonnages offre une plus grande capacité, ce qui signifie que l'entreprise n'a plus à limiter sa production globale. Cependant, le magasin ne satisfait pas seulement l'aspect financier ou le désir d'une plus grande rentabilité. Pour le groupe VPK, la durabilité et l’amélioration de l’impact environnemental ont également joué un rôle majeur. Grâce à un important système de collecte des eaux de pluie, le site de Saint-Quentin est désormais autonome en termes d'approvisionnement en eau. L'installation a été conçue avec prévoyance et dispose d'une capacité suffisante pour faire face à une croissance future de 50 %