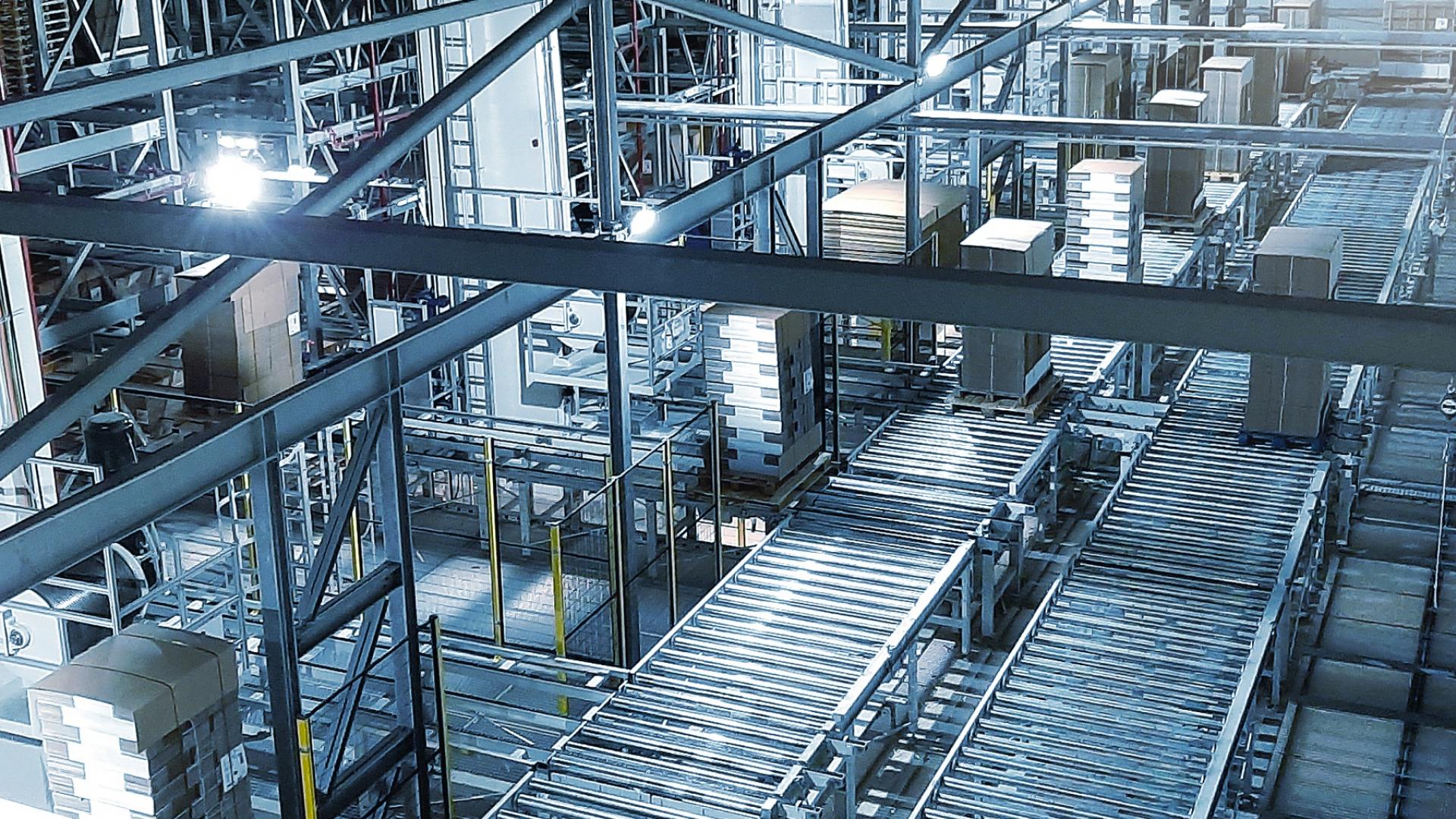
An unprecedented project in France's corrugated industry
High costs due to externally rented storage space, damage during transport, complicated processes in the supply chain, and the desire for a better environmental balance – these were the factors that moved VPK France to build a 6,000-square-meter automated high-bay warehouse next to its production facility in Saint-Quentin in the Hauts-de-France region. Founded in 1935, the family-owned company offers a wide range of customized solutions for packaging made of corrugated and solid board, cores and edge protectors.
Corrugated board – a product with many challenges
VPK manufactures corrugated board in Saint-Quentin – a product that, due to its nature and the large number of different formats, takes up a lot of space for comparatively little value. Accordingly, problems with storage design and workflows are not uncommon. The storage of corrugated board generates high costs – especially if this is done using rented external space, as was the case at VPK. This is because it always requires additional means of transport, such as trucks or forklifts, to move the product from the factory to the warehouse. This not only had a negative impact on the supply chain, but also on the environment – a major issue for the VPK Group, which is strongly committed to sustainability.
A decision matures
In order to stop relying on external storage space, VPK decided to expand its production site with an automated high-bay warehouse. With this, the company wanted to create more storage capacity, avoid bottlenecks and offer its customers maximum quality. A suitable partner for the project was quickly found: The French national subsidiary of the intralogistics expert viastore, which is located in Saint-Jean-de-Braye near Orléans. As a general contractor with more than 50 years of experience, viastore offers comprehensive process know-how, state-of-the-art system technology and, with the viadat Warehouse Management System (WMS), a leading software solution for networked and automated material flows.
VPK was certain: only with an automated warehouse can dynamic and permanent transparency of all stock levels as well as high product quality be guaranteed. "Statistically, the main cause of corrugated board with impaired quality is fork joints and bumps during handling. This is circumvented with an automated system – because it means there is no more manual intervention until the truck arrives," says Philippe Tran, VPK's general manager for France, explaining the advantages of the automated high-bay warehouse.
Production and storage become neighbors
viastore implemented a double-deep high-bay warehouse with six aisles for VPK, which offers space for up to 25,000 pallets on a total of 6,000 square meters and measures 37 meters in height a warehouse size never before seen in the corrugated board sector in France.
Thanks to its direct connection to the plant, the warehouse can directly accommodate the internal production flow. Both finished and semi-finished products are stored. More than 40 different types of pallets are used at VPK, including the Euro pallet. Due to this variety, an intermediate step is required before storage and retrieval: Before the customer pallets are stored, a gantry robot packs them onto slave pallets to standardize the different formats. Then the six stacker cranes, which are optimized for the different pallet sizes, picks up the pallets - a fully automated process.
For goods issue, the pallets are transported via the automatic conveyor system to two preparation zones. There, two robots separate the various customer pallets from the slave pallet before they are distributed to the eight different loading ramps in the shipping area. The special feature here is that picking is based on a sequence calculated by algorithms. The pallets are picked in exactly the order in which they are needed and then prepared on recessed floor conveyors – simulating the loading of a truck. Once the load is complete, it is transported via the floor conveyor to the forklift driver, who only has to load the pallets into the truck in the correct order – a true "goods-to-person" principle. During the loading process, photographs are automatically taken to illustrate that it has taken place without incident.
WMS viadat controls the processes and manages the warehouse
The items in the warehouse as well as all transports and work processes are managed and controlled by the viadat Warehouse Management System (WMS). The intuitive warehouse management system was developed by viastore SOFTWARE GmbH, a sister company of viastore SYSTEMS, and already has more than 2,500 logistics functions in its standard version, which can be expanded and customized to meet specific customer requirements. The main tasks of viadat in VPK's warehouse are the control of input as well as output of finished and semi-finished products and the management of incoming and outgoing slave pallets. Here, the system organizes continuous control of the pallets based on the incoming delivery calls in real time according to the FIFO principle (first in - first out). Thus, the sooner a pallet is for delivery, the further forward it is placed on the shelf. This principle is extremely difficult to implement in a manual or forklift-operated warehouse.
Furthermore, viadat handles the stacking of empty customer pallets and their return. Customer returns are also handled with the help of the warehouse management system. Thanks to its standard interface, viadat is always in close contact with the ERP system GesPack, which VPK uses.
Warehouse capacities increased, CO2 footprint improved
Immediately after commissioning of the pallet warehouse, the benefits become obvious: Thanks to automation, damage to the product is avoided, palletizing has better quality and the individual pallets can be identified more precisely. "Thanks to viadat, there is significantly greater transparency. Employees know where each pallet is at all times. VPK's entire logistics chain is now much more reliable and efficient than before," summarizes Frédéric Juillet, the viastore SYSTEMS IT project manager responsible for the project.
By gradually dissolving the external storage areas, VPK will save costs in the long run. In addition, the high-bay warehouse offers more capacity, which means that the company no longer has to limit its overall production. However, it is not only the financial aspect or the desire for more profitability that is fulfilled with the warehouse: Sustainability and a better carbon footprint for the VPK Group also played a major role: thanks to a large rainwater collection system, the Saint Quentin site is now autonomous in terms of water supply. The facility was designed with foresight and offers enough capacity to absorb a future growth of 50 percent.