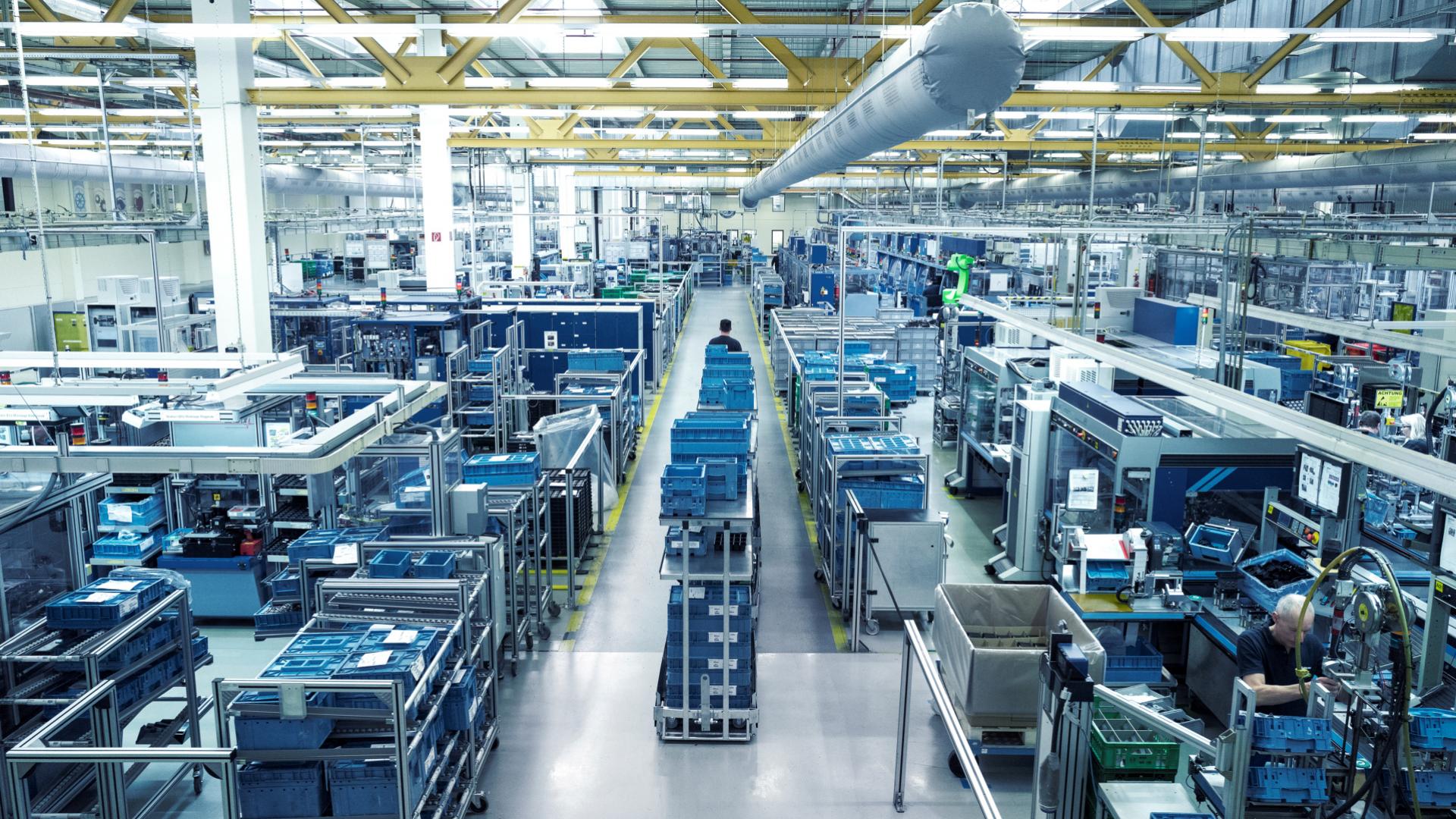
Intralogistik in der Montage- und Produktionsversorgung
Optimierungspotential in der Montage- und Produktionsversorgung
Die Montage- und Produktionsversorgung ist ein wichtiger Bestandteil der Intralogistik. Sie umfasst sowohl den innerbetrieblichen Transport, den Umschlag und die Lagerung als auch die Kommissionierung. Damit es bei der Produktion und Montage zu keinen Warte- oder Fehlzeiten kommt, lagern viele Betriebe Waren, die sie dort benötigen, auf Vorrat ein. Dies führt jedoch zu einem hohen Bestand und zu einem großen Bedarf an teurer Lagerfläche – Umstände, die sich negativ auf die Leistung, Effizienz und Wirtschaftlichkeit des gesamten Betriebs auswirken.
Für Industrieunternehmen liegt in der Montage- und Produktionsversorgung damit aber nicht nur ein großer Kostenfaktor, sondern auch ein großes Optimierungspotenzial. Mit gezielten Logistikmaßnahmen können Sie Prozesse schlanker und flexibler gestalten und gleichzeitig Ausgaben und benötigte Logistikfläche erheblich reduzieren.
Unter der „Just in time“-Versorgung versteht man ein Konzept zur Verbesserung der Waren- und Beschaffungslogistik. Der Beschaffungsvorgang innerhalb der Produktionskette wird dabei so gesteuert, dass genau in dem Moment, in dem der Bedarf entsteht, neue Waren an die Produktions-und Fertigungseinheiten angeliefert werden. Eine wichtige Rolle spielt dies beim Versand, der Produktion und bei der Montage.
Eine „Just in time“-Montageversorgung hat für Industrieunternehmen erhebliche Vorteile: Anwender können ihre Lagerbestände deutlich reduzieren und sowohl die Durchlaufzeiten verringern als auch kostenintensiven Lagerplatz einsparen. Dies verbessert die Lieferfähigkeit und führt so zu einer Steigerung der Wettbewerbsfähigkeit.
Um das „Just in time“-Konzept umzusetzen und einen stetigen Materialfluss zur Versorgung der Montageplätze zu gewährleisten sowie Stillstandzeiten zu vermeiden, ist eine effiziente Planung, Lagerung und Steuerung notwendig. Ein Pufferlager oder auch Kurzzeitlager, in denen die Waren nur für kurze Zeit zwischengelagert werden, in Verbindung mit einem Lagerverwaltungssystem oder Warehouse Management System (WMS), stellt hier eine platzoptimale Lösung dar. Durch das WMS, welches die zentrale Verwaltung und Steuerung der gesamten Intralogistik übernimmt, kann besonders schnell auf Bestandsveränderungen reagiert werden und somit ein schlanker Montageprozess sichergestellt werden.
Die GROB-Werke GmbH & Co. KG. mit Hauptsitz in Mindelheim hat sich für eine solche Lösung entschieden. Das Familienunternehmen ist Anbieter von kundenspezifischen Gesamtlösungen in der Großserienfertigung, bestehend aus modular aufgebauten Bearbeitungszentren und Sondermaschinen, die durch moderne Automatisierungslösungen verkettet sind. Dazu gehören beispielsweise Zerspanungsanlagen für die Automobilindustrie, Montageanlagen im Bereich Powertrain, aber auch Universal-Bearbeitungszentren für Zulieferer. Im Lauf der Zeit reichten die Lagerkapazitäten nicht mehr aus, um die Montagearbeitsplätze zuverlässig zu versorgen. Zudem wurden der Warenfluss und die Bestände durch die manuelle Bearbeitung zunehmend intransparent. Durch die Installation eines automatischen Kleinteilelagers (AKL) und einem automatischen Palettenlager konnte GROB einen effizienten Materialfluss zur Versorgung der Montagearbeitsplätze sicherstellen.
Um die Prozesse in den neuen Anlagen möglichst effizient zu steuern, setzt GROB neben SAP auf ein Warehouse Management System, welches direkt an SAP gekoppelt wird. Das WMS konzentriert sich in diesem Fall auf die Vergabe und die Verwaltung von Lagerplätzen und regelt die Fahrstrategien für die Ladeinhalte im RGB des Logistikzentrums. Damit gleicht es Bestandsveränderungen „just in time“ aus und optimiert so den gesamten Montageablauf. Ein weiterer Vorteil: Mit dem WMS lassen sich sämtliche Waren und Prozessabläufe lückenlos zurückverfolgen, das Risiko für Schwund ist dadurch wesentlich geringer. Die Modernisierung bringt für GROB zusätzlichen Nutzen: eine höhere Flexibilität bei der Lagerung von kleinen Teilen sowie eine deutlich höhere Platzausnutzung. Durch die neue automatische Lösung hat sich nicht nur die Kommissionierqualität verbessert, sondern auch die Umschlagsgeschwindigkeit deutlich erhöht. Die optimierte Anlagenverfügbarkeit stellt zudem eine prozesssichere Montage sicher.
Reduzierung von Umlaufbeständen senkt Kosten
Einen hohen Kostenfaktor für viele Industrieunternehmen bilden kapitalbindende Umlaufbestände.
Die wesentliche Ursache dafür liegt vor allem in einem starken Sicherheitsdenken. Denn Umlaufbestände dienen als Puffer, der bei möglichen Fehlplanungen oder Lieferschwierigkeiten einen Schaden ausgleichen und für eine unterbrechungsfreie Produktion oder Montage sorgen soll. Zu hohe Umlaufbestände verdecken allerdings Schwachstellen in der Organisation. Um die Bestände, die sich zwischen den einzelnen Arbeitsschritten ansammeln, zu minimieren, ist es wichtig, die Auftragsabwicklung in Verbindung mit den Produktionsprozessen zu optimieren.
Auch hier bietet eine Lagersoftware wie z.B. das Warehouse Management System, welches GROB im Einsatz hat, eine Lösung. Die moderne Standardsoftware regelt zuverlässig und effizient den kompletten Materialfluss in konventionellen und automatischen Lagern, Kommissionieranlagen sowie Distributions- und Logistikzentren. Durch die zentrale Steuerung der Lagerstationen und Produktionsschritte erkennt das WMS besonders schnell Fehlstände oder zu hohe Umlaufbestände und kann diese selbständig ausgleichen oder reduzieren. Hohe Pufferbestände lassen sich damit vermeiden und Kapital, das bisher in den Vorrat investiert wurde, wird für weitere Investitionen frei. Die Lagersoftware reduziert darüber hinaus auch Fehler beim Bestellen, Kommissionieren und Lagern auf ein Minimum, sorgt für schnellere Durchlaufzeiten und eine bessere Transparenz aller Bestände.
Rohwaren- und Halbfertigzeuge-Lagerung
Die Ansprüche an Rohwaren- und Halbfertigzeuge-Lager sind hoch: Sie müssen nicht nur viel Kapazität aufweisen, sondern müssen sich auch sehr flexibel be- und entladen lassen, damit das Unternehmen möglichst schnell auf kurzfristige Bestellungen reagieren kann.
Vor dieser Herausforderung stand die Gebrüder Müller Apparatebau GmbH & Co. KG (GEMÜ) mit Sitz im baden-württembergischen Ingelfingen. Der führende Hersteller von Ventil-, Mess- und Regeltechnik hat eine Produktpalette mit mehr als 400.000 möglichen Varianten, die von Kunden aus unterschiedlichen Branchen nachgefragt wird. Eine Kernkompetenz des Unternehmens sind aus Vollmaterial gefräste Mehrwege-Ventilblöcke. Die GEMÜ-Produkte entstehen in modernen, klar strukturierten Produktionshallen mit innovativen Fertigungsmethoden an ergonomischen Arbeitsplätzen.
Hier passte das veraltete Logistik-System nicht mehr zu den neuen Geschäftsprozessen. Die manuelle Ver- und Entsorgung der Arbeitsplätze bewerkstelligten die Mitarbeiter mit Hubwagen. Sie richteten kleine Pufferlager ein und bewegten dadurch jeden Tag mehrere Tonnen Material von Hand. Das war nicht nur zeit-, sondern auch besonders kostenintensiv. Die Lösung brachte ein neues Produktions- und Logistikzentrum.
Um die Prozesse beim Be- und Entladen der Rohmaterialien effizienter zu gestalten, setzt GEMÜ auf ein automatisches Palettenlager zusammen mit einem automatischen Kleinteilelager, welches über einen Behälterloop an die Kommissionier- und Versandhalle angebunden ist. Für die Steuerung aller Logistik-Prozesse bei GEMÜ sorgt ein WMS. Es managt den Materialfluss vom Wareneingang der Komponenten über Lagerung, Auslagerung und Versorgung der Produktion bis hin zur Kommissionierung und Versand. Das WMS regelt darüber hinaus die Pufferung der Montageversorgung, um ausreichend Druck auf die Montageplätze geben zu können. Mit der neuen automatisierten Lagerlösung ist es GEMÜ gelungen, Rohwaren deutlich effizienter, flexibler und platzsparender zu lagern und zu transportieren. Das entlastet nicht nur die Mitarbeiter von schwerer, monotoner und nicht-ergonomischer Arbeit und reduziert zudem die Unfallrate, sondern senkt auch die Kosten für die Lagerung.
Bestandsreduzierung im Lager
Auch zu hohe Lagerbestände werden von einem stark ausgeprägten Sicherheitsgedanken verursacht. Materialbestände im Beschaffungs-, Produktions- oder Distributionslager haben die Aufgabe, Engpässe auszugleichen und flexibel auf Planungsänderungen zu reagieren. Die Lagerung der kapitalbindenden, überschüssigen Waren ist jedoch kosten- sowie zeitintensiv und beansprucht teure Lagerkapazität – die deutlich effektiver genutzt werden kann.
Eine Bestandsreduzierung im Lager hat zudem nicht nur das Ziel, Platz für neue Verkaufsprodukte zu schaffen, sondern auch die Wettbewerbsfähigkeit eines Unternehmens aufrechtzuerhalten. Denn eingelagerte Artikel sind nicht verkauft, und ihr Wert kann in der Zwischenzeit sinken.
Ein erhebliches Rationalisierungspotenzial steckt für Unternehmen mit hohen Lagerbeständen in der Automatisierung der Logistik. Das veranschaulicht das Beispiel der Werda GmbH & Co. KG aus Finnentrop, die sich auf die Produktion von kundenspezifischen Augen- und Hammerschrauben spezialisiert hat. Das Lieferspektrum des Unternehmens war über die Jahre auf rund 25.000 Artikel gestiegen, von denen etwa 6.000 ständig im Lager bevorratet wurden. Darüber hinaus übernahm Werda immer mehr auch die Lagerhaltung für die belieferten Händler. Damit wuchs nicht nur die Artikelzahl, auch die hierfür benötigte Lagerfläche für die Halbfertigteile und fertigen Waren erforderte immer mehr Platz. Die Lagerung war auf fünf verschiedene Hallen verteilt und erfolgte nach dem Prinzip „Person zu Ware“.
Die Folge waren lange Laufwege und verzögerte Prozesse, da eingelagerte Artikel oftmals nicht auf Anhieb von den Mitarbeitern gefunden wurden. Gefordert war ein neues System, das die Wege verkürzte und damit die Flexibilität und Reaktionszeit erhöhte. Das Unternehmen benötigte zudem mehr Platz für die mechanische Bearbeitung. Hallenflächen, die dafür vorgesehen waren, wurden teilweise vom Lager belegt. Die optimale Lösung fand Werda mit einem automatischen Lagersystem, das aus einem Tablarlager und der passenden Lagerverwaltungssoftware bestand. Letztere ließ sich problemlos an das bestehende ERP-System anbinden. Dessen Aufgabe besteht darin, die Summenbestände zu verwalten und entsprechende Bestellvorgänge auszulösen, während die Lagersoftware die Verwaltung der Einzelbestände übernimmt. Das eingassige Tablarlager mit 5.986 Stellplätzen schmiegte sich auf einer Länge von etwa 64 Metern und einer Höhe von 10 Metern optimal an eine vorhandene Halle an.
Mit dem automatischen Lagersystem ist es Werda gelungen, die Lieferqualität zu verbessern sowie Waren deutlich schneller und flexibler zu versenden und damit den Bestand zu reduzieren. Darüber hinaus hat das Unternehmen viel Platz in den Hallen geschaffen, den es für eine Ausweitung und Neustrukturierung der Produktion nutzen kann, um weiter zu wachsen und seine Position im Markt zu behaupten.