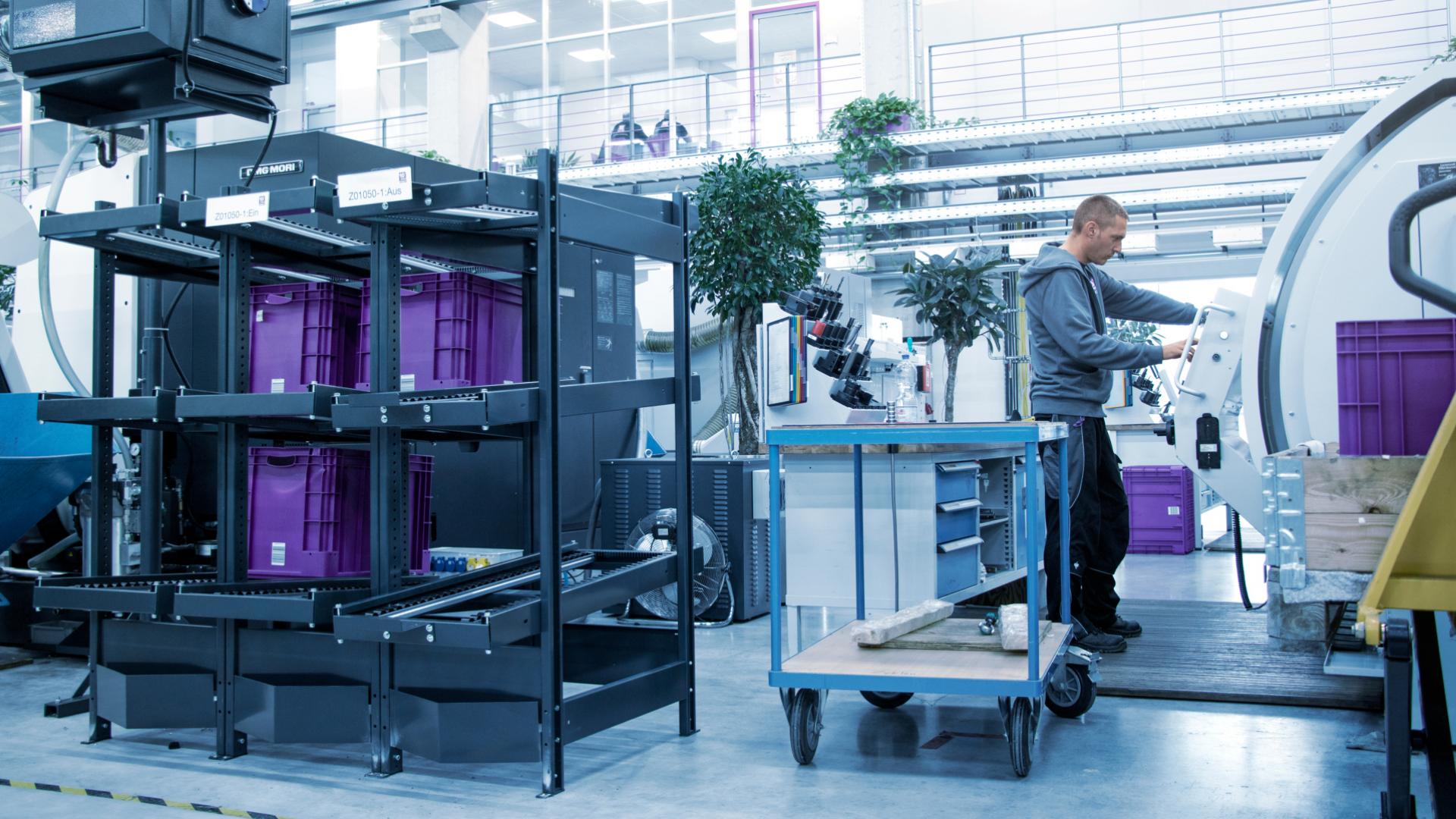
Connecting warehouse and production for the Smart Factory
With WMS and MES integration for more efficiency in the manufacturing industry
One of the goals of Industry 4.0 is to increase transparency and efficiency in logistics and production – among other things, through the functional integration of both areas. The processes of logistics and production are considered "integrated" today, but in reality they still go their separate ways in many companies. Often there are only points of contact at the transfer points of material and goods. The consequences are non-transparent and cumbersome processes, excessive inventories and work in progress stocks as well as loss of time and quality. Efficient production and batch size 1 are wishful thinking.
But this does not have to be!
The integrative connection of warehouse management (WMS), transport control (WES) and production control system (MES) enables more transparency and efficiently interlinked processes. The Warehouse Management System (WMS) can be connected to all common Manufacturing Execution Systems (MES) via its standardized interface – and thus enables the efficient connection of logistics and production. This increases customer satisfaction and frees up tied capital for important investments.
Increase transparency and efficiency holistically!
viadat's standard interface to all common Manufacturing Execution Systems (MES) enables you to network material flows across traditional borders and to integrate logistics and production processes. Both systems are equal partners but use and generate different information. The MES knows what and how much each machine produces and which material is required at which location in production or can be removed.
The WMS knows where the required materials are stored and controls the supply and disposal of material as well as the transport between the production lines. It knows the means of transport, their characteristics and the topology of the facility and can therefore control the optimal routes, routes and times for transporting goods. By combining the two systems, you benefit from lower work in progress stocks, shorter throughput times and true traceability of goods, even in the smallest sizes.
The benefits:
- True traceability for real-time parts tracking along the entire material flow in logistics and production
- Visualization of the material buffers between the operations
- Precise forecasting of an expected buffer stock history
- Automatically updated ONLINE monitoring of the production facilities
- Complete batch tracing
- Event-driven alternative transport sequences
- Variable transport units per process
- Expiration time as a trigger for transport
- No unnecessary forklift trips (empty runs)
- Material planning for short-term production requirements
- Management of minimum storage periods as well as shelf life and expiration dates
- Range calculation of material intermediate products and semi-finished products
- Control of eKanban and transports
- Order-based estimation of the transfer requirements for the next shift
- Exact forecast of the expected buffer stock
- Better use of resources
- Improved production planning
- High efficiency even with small batch sizes