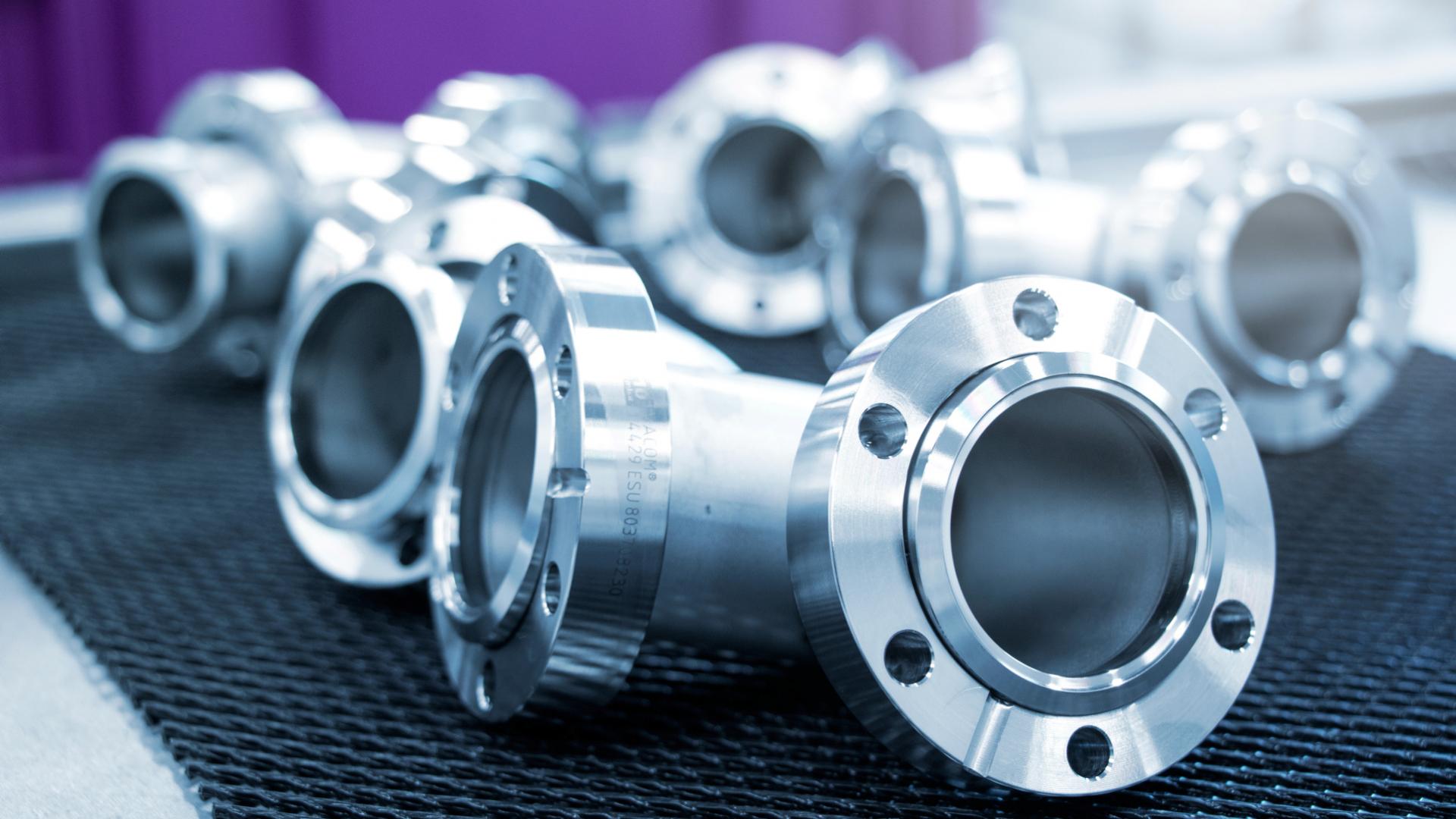
Logistik und Produktion werden eins
Verknüpfung von WMS und MES schafft Voraussetzung für „Smart Factory“
„Je mehr Bauteile wir fertigten und je komplexer die Produktion wurde, desto mehr wurde sie zu einem schwarzen Loch“, erinnert sich Kevin Mahler, COO bei der VACOM GmbH. Das 1992 gegründete Unternehmen mit Sitz in Jena fertigt Komponenten für Anwendungen im Hochvakuum bis ins extreme Ultrahochvakuum. Mit Erfolg, denn der Bedarf an ultra-reinen Vakuumbauteilen besteht in immer mehr Branchen – zum Beispiel in der Forschung, bei der Chipherstellung oder für die Beschichtung von Optiken und Displays. Allein in den vergangenen eineinhalb Jahren ist das Unternehmen um mehr als 100 Personen gewachsen. Heute beschäftigt VACOM rund 350 Mitarbeiter, hat 120 weitere Stellen ausgeschrieben und gehört zu den führenden europäischen Anbietern von Vakuumtechnik.
Das rasante Wachstum stellt das Unternehmen vor neue Herausforderungen: Die Prozesse effizient zu managen und zugleich den Überblick zu behalten, bedeutet großen Aufwand. „Unsere Produkte sind äußerst komplex – sie bestehen teilweise aus mehreren hundert Komponenten“, erklärt Mahler. Die meisten dieser Komponenten, wie zum Beispiel Flansche, produziert VACOM selbst – in Losgrößen von bis zu 1.000 Stück.
„Komplexe Produkte wie unsere Kugel- oder Zylinder-Vakuumkammern fertigen wir maßgeschneidert nach Kundenanforderung.“ Die typische Losgröße liegt hier bei einem bis maximal zehn Stück – „serienmäßigen Prototypenbau“ nennt Kevin Mahler das. Die Halbfertigteile wechseln im Fertigungsprozess wiederholt zwischen den einzelnen Arbeitsschritten und Werkzeugmaschinen hin und her. Eine klassische Linienfertigung ist damit nicht möglich. Auch klassische Produktionssteuerungssysteme wie Kanban sind bei VACOM nicht anwendbar, da an einer Station selten das gleiche Bauteil benötigt wird.
Daher mussten die VACOM-Mitarbeiter zu Beginn einer Auftragsbearbeitung das benötigte Material vollständig zusammenstellen und anschließend über die verschiedenen Maschinen und Arbeitsplätze verteilen.
Materialsuche frisst zu viel Zeit
„Wir haben die Halbfabrikate und Rohmaterialien in die Fertigung gegeben und bekamen ein Endprodukt heraus“, beschreibt Mahler. „Zwar wussten wir, was in der Produktion passierte, aber nicht, wo sich die einzelnen Materialien zu welchem Zeitpunkt genau befanden.“ VACOM konnte daher nur schwer auf Änderungen reagieren.
„Unsere Mitarbeiter verbrachten zunehmend Zeit damit, Bestandteile zu suchen und an ihren Arbeitsplatz zu schaffen. Das ging schließlich soweit, dass wir pro Schicht mindestens einen Kollegen hatten, der nichts anderes tat, als Material zu suchen“, resümiert Kevin Mahler. Bei einer Produktionsmannschaft von damals 50 Personen war das eindeutig zu viel.
VACOM entschied sich daher, die Produktion in eine „Smart Factory“ zu verwandeln. Dazu generierte Mahler mit seinem Team zunächst eine transparente Fabrik: In einem digitalen Abbild haben sie definiert, wie die einzelnen Komponenten durch die Fertigung laufen sollten und welche Arbeitsschritte hierbei durchzuführen sind. „Erst dann wird ersichtlich, wo sich was befindet, was aktuell gemacht wird und wer an welcher Maschine arbeitet“, legt Kevin Mahler dar. Diese Daten bildeten die Basis für die zweite Stufe auf dem Weg zur intelligenten Fabrik – die Schaffung einer reaktionsfähigen Produktion. Dafür setzt VACOM zum einen auf das Manufacturing Execution System (MES) HYDRA der MPDV Mikrolab GmbH und zum anderen auf das Warehouse Management System (WMS) viadat von viastore SOFTWARE, welches bereits das bestehende Automatiklager verwaltet. Das gemeinsame Datenmanagement von WMS, MES und SAP ERP ermöglicht es, schnell auf Kundenänderungen oder neue Bedürfnisse zu reagieren.
2019 folgte die nächste Stufe zur Smart Factory: die selbstregelnde Fabrik. Zunächst beabsichtigte Kevin Mahler eine durchgehende Automatisierung der Produktionslogistik und infolgedessen die Nutzung von Transportrobotern. Dazu wandte er sich an viastore: „Die Fachleute erklärten, dass der Einsatz von Transportrobotern in viadat Standard sei.“ Allerdings ging es in diesem konkreten Fall um die logistische Versorgung der Produktion. Dies bedeutete, dass das WMS nach jedem Arbeitsschritt einen Auftrag vom MES erhalten muss, um die Roboter entsprechend zu steuern. Eine derartige Verknüpfung von MES und WMS existierte bis dato nicht standardmäßig. Doch um genau solch eine Integration zu ermöglichen, hatte viastore bereits einige Zeit zuvor eine strategische Partnerschaft mit MPDV geschlossen – jenem Software-Haus, von dem das MES bei VACOM stammt.
viadat verfügt in der aktuellen Version über eine Standard-Schnittstelle, die den Datenaustausch mit HYDRA ermöglicht. „Über diese Schnittstelle lassen sich auch andere gängige MES-Lösungen mit viadat verknüpfen“, erklärt Simon Kallinger, der für viastore das Projekt bei VACOM geleitet hat. Dazu holte VACOM alle Beteiligten an einen Tisch. Gemeinsam haben sie definiert, wie sie die Systeme im Detail integrieren können und welche Kernkompetenzen sie jeweils erfüllen sollen.
Das Ergebnis war eine enge Integration beider Systeme, „wobei WMS, MES und SAP gleichberechtigte Partner sind und eigene Entscheidungsbefugnisse haben“, betont Kevin Mahler. „Das heißt MES und WMS geben Informationen selbstständig weiter, ohne die Schleife über SAP zu gehen.“ Sie regeln automatisch die Aufgaben für die rund 45 Arbeitsstationen in der Produktion sowie die sechs Transportroboter.
Zwei Systeme, die sich selbst regeln
SAP ist im Zusammenspiel der Systeme letztlich nur noch für die Auftragsgenerierung zuständig und übergibt die Fertigungsorder mit Stückliste an HYDRA. Das MES übernimmt die Feinplanung – welche Maschine, welches Werkzeug, welches Material, welcher Mitarbeiter – und übermittelt anschließend eine Stückliste inklusive Terminierung an viadat. Dieses wiederum generiert Nachschubaufträge für den jeweiligen logistischen Bedarf pro Arbeitsgang, die im Supermarkt-Lager der Produktionshalle gepuffert werden. Dieses reduziert den notwendigen Zwischenlagerplatz an den einzelnen Arbeitsstationen.
Erst kurz vor der Verarbeitung erteilt das WMS einen Transportbefehl, und ein Roboter bringt das Material zur Arbeitsstation. Hier wird es nochmals in kleinen Regalen verwahrt, ehe es endgültig in die Bearbeitung geht. So können die Kapazitäten an den Bearbeitungsmaschinen optimal genutzt werden. Der Werker stellt den fertigen Auftrag auf einem Ausgangspuffer ab und scannt ihn. Das löst wiederum eine Anweisung in viadat aus, so dass ein Roboter die Ware anschließend ins Supermarktlager oder direkt zur nächsten Arbeitsstation bringt.
„viadat tritt also auch zwischen den einzelnen Arbeitsschritten in Aktion, MES und WMS kommunizieren kontinuierlich miteinander“, schildert Kevin Mahler. Simon Kallinger ergänzt: „Wir haben damit ein echtes Just-in-Time-Konzept umgesetzt. viadat kennt die Kapazitäten an den Pufferplätzen und kann somit planen, dass diese durchgehend befüllt werden und das Material rechtzeitig vor dem nächsten Arbeitsgang bereitsteht.“
Das wird einen gewaltigen Effizienzgewinn für die Mitarbeiter an den Arbeitsstationen nach sich ziehen, steht für Kevin Mahler fest. „Die Kollegen werden weder ihr Material zusammensuchen noch Kisten schleppen müssen. Alles was sie für den Produktionsschritt brauchen, bekommen sie direkt an den Arbeitsplatz geliefert. Sie selbst müssen nur noch rüsten und bearbeiten.“ Damit werden sie von anstrengenden und ungeliebten Tätigkeiten entbunden und machen ausschließlich das, wofür sie ausgebildet sind und woran sie Spaß haben.
Das gilt aber nicht nur für die Beschäftigten an den Maschinen, sondern auch für die Fachkräfte, die sich um die Organisation und Abwicklung der Fertigung kümmern. Dank der Transparenz, die sich infolge der Verbindung von WMS und MES ergibt, wissen sie zu jeder Zeit, wo sich welches Material befindet, wie ausgelastet die Maschinen sind und wie weit die Bearbeitung des Produkts vorangeschritten ist. „Ihr Workload wird um ein Vielfaches reduziert“, erklärt Mahler zuversichtlich. „Erst wenn die Systeme bestimmte Probleme nicht lösen können – zum Beispiel, weil ein Zulieferteil im Lager fehlt, – wird ein Mensch zur Hilfe gerufen. Die Mitarbeiter werden also nicht mehr als Hin- und Herschieber von Kisten genutzt, sondern werden zum Problemlöser.“
Gesamte Effizienz erheblich gesteigert
Auch die Kunden von VACOM profitieren von der smarten Fertigung, wie Kevin Mahler erläutert: „Die Bestandsführung ist optimiert, Stillstands- und Liegezeiten werden massiv reduziert. Unsere Kapazität steigt und die Durchlaufzeiten werden sinken. Außerdem können wir unsere Kunden schneller beliefern.“
Allein mit dem Stand der selbstregelnden Fabrik ist die OEE, die Overall Equipment Effectiveness, in der Produktion von VACOM zwischen fünf und zehn Prozent gestiegen. Kevin Mahler geht von weiteren fünf bis zehn Prozent aus, wenn die jetzige Optimierung abgeschlossen ist, und ist sich sicher: „Nur wer schnell und flexibel auf Kundenwünsche reagieren kann, ohne dass Chaos entsteht, bleibt langfristig am Markt erfolgreich. Produktion und Logistik als verschiedene Paar Schuhe zu betrachten, wird in Zukunft nicht mehr funktionieren.“