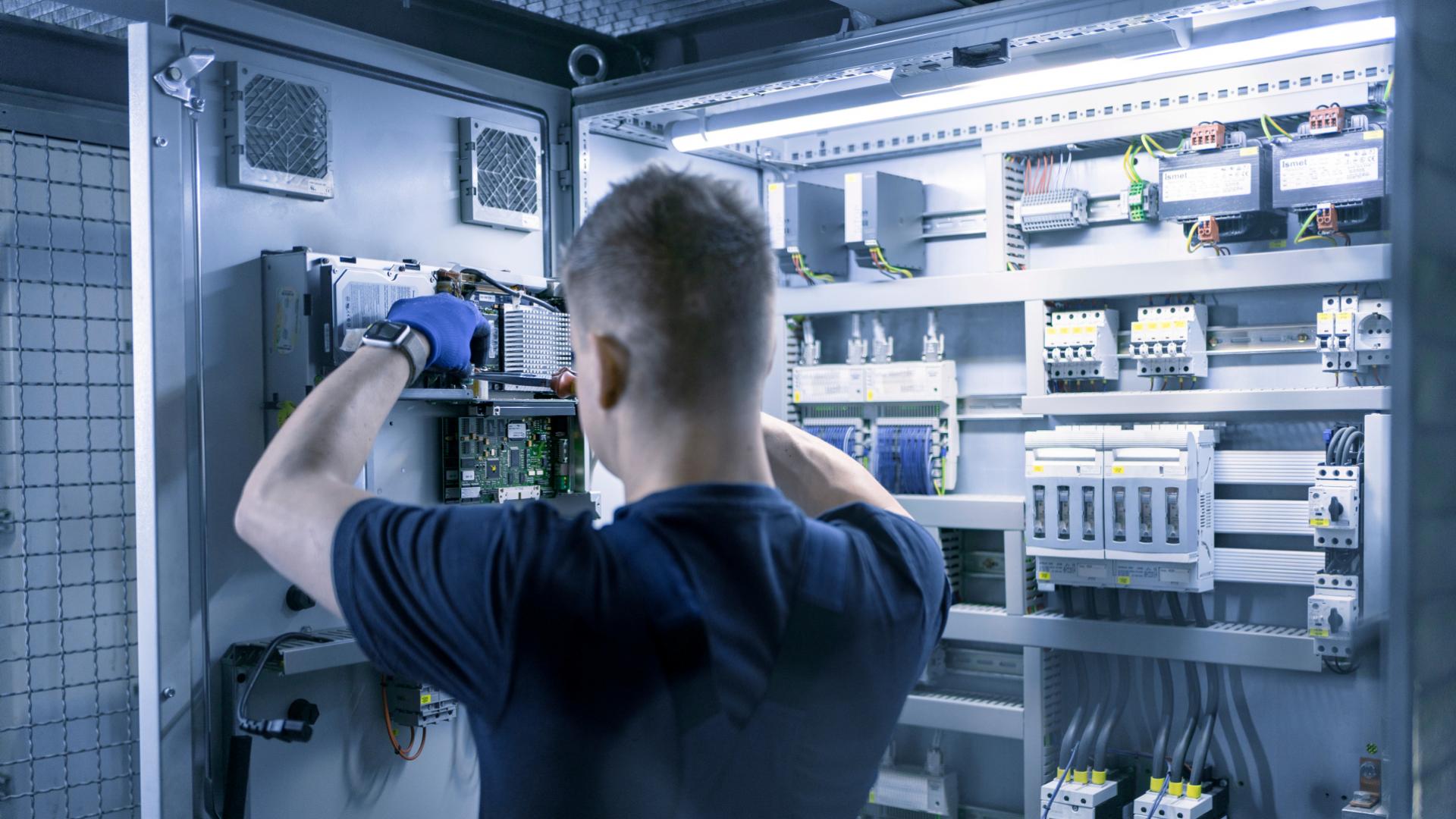
Then vs Now:
50, even 25, years ago, almost all material handling systems, whether a fleet of lift trucks, a carton sortation system, or an ASRS, could function with limited maintenance. Overbuilt, over spec, and over delivered solutions produced excess capacity and capabilities that could erode over time with little or no maintenance without stopping production. Swap batteries, replace power bands, or a simple annual inspection and fluid change was more than enough to keep the system going. But today, with integrated systems, software updates, and computerized management systems, you need to perform preventive maintenance, not just routine reactive maintenance.
Why?
First, control systems have become more computerized. Raymond, an arm of the Toyota Automated Logistics Group, has onboard data collection and collation in its telematics packages. This allows for tracking performance data like battery health, motor conditions, even things like idle vs active usage. But every one of those abilities has sensors, cabling and programming that needs to be checked. viastore, over time, has converted to much more capable PLCs that can monitor motor conditions, verify the alignment of loads, and validate the ID of the load on each crane as it is moved. Again, sensors, cabling, and programming were added to add this valuable operating information.
This additional functionality comes at a cost. It means that you have to check these items in more detail, earlier and more frequently to ensure uptime. This increased tempo of inspections allow for things like motor faults, loose wiring, or misaligned sensors to be caught before they become truly broken systems.
Second, new technologies, or at least new to your company, have a learning curve for usage. When a new system is delivered, it Is configured to run optimally for the material, volumes, and processes it was designed for. But there is two factors that are not included in the design, the labor and new product . From overloading equipment to damaging structures, even misusing logic, personnel, even after training, will still put wear and tear on the system. New products (or even changes in packaging) can create new stresses or the need for workarounds in the equipment. Preventive maintenance is key to seeing what, how, and why that wear is appearing. A pallet lift can be overloaded in its weight capacity repeatedly, but still function. The problem the overload causes to the concrete floors or to the pneumatics over time will not be seen until catastrophic failure occurs. That label printer is "faulting" but the issue may be the surface of the carton it is touching. But when you have the equipment inspected regularly, and attention is paid to the wear patterns, you gain time to plan real solutions to the changing usage of the new equipment.
This especially applies to software. It may appear that software updates are merely improving security or patching over bugs. In reality, MHE software updates can allow for remote monitoring capabilities, intelligent logic improvements, even better reporting options. Even software updates in seemingly unrelated areas need to be managed in regards to the material handling systems. The process of deciding if an update is needed, when to do the updates, how to test both new features and old capabilities, and when that update goes from optional to essential needs the input of more than the internal maintenance and IT groups, but also the experts, the equipment providers. And that occurs when those providers are onsite looking at preventive maintenance findings.
Third, even the best trained internal maintenance department can't know every new technology. As the equipment becomes less tolerant of misuse and more sensitive to monitoring, the old solutions that "have worked for years" just can't keep up. Knowing the operating needs of the new system now requires a depth of experience with that type of equipment that the MHE integrator or manufacturer only has. Such minor issues as air pressure drops, voltage changes, or even altered active shift schedules have impacts on the performance of many types of material handling equipment. Knowing what subsystems could be affected and what options exist to minimize the impact is hard to acquire, but vital to keeping the new system running well. Preventive maintenance allows the technical expertise of the equipment provider to put "eyes on" the issues and find long lasting resolutions.
Finally, maintenance itself has evolved from a reactive only discipline to a more nuanced model. Replacing worn parts or problematic components only when they fail has always created system down time. But with many material handling solutions having critical subsystems that can't be offline, this type of maintenance is intolerable. The single pallet conveyor into the warehouse from the freezer is key to your operation. The single lift that reaches the floors of your facility can't break. They can't wait for failure. The newest approach to maintenance tries to address this with prevention and, in some cases, predictive options.
Preventive maintenance focuses on inspection, lubrication, and measurement of key parts to reduce the chance of failure. ASRS systems need transmission oils change regularly, but also the wire rope inspected for unusual wear, stretching, or deformation. Wiring harnesses, sensors, and even physical controls need to be inspected and tested. And even the condition of hardware like wheels, guides and beams should be examined. It is much easier and cheaper to plan a scheduled replacement of major components weeks or months in advance that it is to respond overnight to an emergency.
Predictive maintenance is the latest frontier for keeping a system running optimally. This type of approach focuses on replacing components before they can fail, using data and in depth knowledge from other installations. While this may appear more expensive to the customer as a running expense, the reality is that the downtime and loss of production can be minimized best by avoiding surprises. The best approach, from industry experience, seems to be a balance of prevention and prediction to stay ahead of wear and misuse.
The need for a range of maintenance options that applies to the range of equipment, areas of scrutiny, and actual needs of the facility is vital to maintaining your uptime. Keeping with the "tried and true" can risk critical failures at the worst times, but being proactive can help to find those critical areas, plan for unobtrusive maintenance, and help maintain the production capacity of any facility. Prevent degrading equipment or exposed security concerns, predict when replacements are needed, and do not wait for an "unintended facility shutdown" to determine how to avoid maintenance downtime events.